Как обложить печь в бане кирпичом — ВикиСтрой
Выбор кирпича и связующего
Кирпичный экран каменки несёт не только защитную, но и декоративную функцию. Поэтому брать на кладку всё, что попадётся под руку, явно не стоит — лучше уделить внимание подбору материалов, даже если это сопряжено с дополнительными затратами.
Кирпич, к примеру, обязательно должен быть полнотелым — экран должен хорошо и быстро накапливать тепло. Правда, от футеровочного шамота марок ПБ или ША всё же лучше отказаться: от их огнеупорных свойств толку мало, да и вид не особо притязательный. Ну а поскольку плотность кирпича должна быть умеренно высокой, чтобы кладка успевала прогреваться, то оптимальным вариантом можно назвать красный глиняный печной кирпич марки М-200.
0Облицовочная серия такого кирпича включает ряд специальных изделий, предназначенных для выполнения кладки с высокой эстетической ценностью. Используя угловой кирпич вместе с рядовым, а также колотый, рифлёный и профильный, можно добиться высокой индивидуальности вида вашей каменки.
Связующим в обкладке экрана выступает смесь шамотного мертеля марки МШ-18 и ЦПС. Мертель мешается с речным песком в равных частях и замачивается в течение 2–3 суток. Цемент марки 400 выступает ускорителем схватывания, его добавляют непосредственно перед кладкой в количестве 1/4 от объёма сухой смеси мертеля и песка. Чтобы придать кладке более изысканный вид, раствор можно тонировать мелом, суриком, охрой или сажей.
Подготовка основания, стен
Самый подходящий момент для сооружения экрана — когда парилка ещё не отделена от предбанника перегородкой. Другой вариант — перегородка уже возведена, но в нижней части имеется проём для тоннеля топки. Впрочем, если топка обращена внутрь парилки, обкладывать печь можно в любое удобное время.
Намного более важный момент — подготовка основания под кладку. Ввиду значительного собственного веса каменка требует бетонного постамента, но его не всегда отливают с дополнительным выпуском по сторонам. Кирпичный экран не особо тяжёлый, но ему обязательно нужно придать монолитность. Поэтому если выступ постамента под каменкой меньше 160 мм, потребуется отливка опоясывающей ленты.
В некоторых случаях допускается отливать ЖБ-изделие прямо по полу, соорудив внешнюю опалубку по периметру печи. Даже деревянный пол при достаточно добротном устройстве способен выдержать 300–350 кг распределённой нагрузки. Ленту следует отливать почти вплотную к корпусу печи шириной на 50–60 мм больше кирпича, то есть около 170–180 мм. Минимальная высота ленты ограничивается защитными слоями бетона, для помещения это около 25 мм сверху и снизу, то есть 50 мм в целом плюс толщина арматуры. Армировать лучше сталью, например, 8 мм профильным прутком А500С в три ряда с отступом по 40–50 мм.
Каменка может располагаться вплотную к одной или двум стенам. Экран в таком случае выкладывается примыкающим, но от стен печь обычно кладкой не ограждают. Если обшивка в этих местах выполнена горючим материалом, например, деревянной вагонкой, её лучше сразу обрезать на метр выше печи. Также возможен вариант с экранирующей теплоизоляцией из жестяного листа и магнезитовой или асбестовой прокладки под ним.
Размещение печи: вариант с вынесенной топкой
При отсутствии вынесенного топочного люка печь может находиться в любом удобном положении, которое обычно определяется расположением дымохода. Если расстояние до стен меньше 200 мм, печь не обкладывают со всех сторон или ограничиваются бутовой кладкой в четверть. При большем отступе рекомендуется выкладывать кожух со всех сторон.
Если печь имеет выносную топку, её лучше устанавливать и обкладывать, когда парилка ещё не отделена перегородкой, либо же в перегородке заранее подготовить проём высотой на 30–40 см больше печи. Основные правила размещения и ориентации корпуса относительно проёма имеются в большинстве монтажных инструкций, прилагаемых к каменкам.
Зачастую печь устанавливается передней стенкой корпуса в одной плоскости со стеной парилки. Если топочный люк выступает над плоскостью стены с обратной стороны, печь смещают назад или подрезают тоннель. Устанавливать каменку частично в сечении стены категорически нельзя.
Кладка экрана
Обкладка каменки выполняется в полкирпича с перевязкой между рядами не менее трети длины. Как показывает практика, это самый эстетичный вариант, к тому же так намного легче образовать бойницы для забора воздуха. Камни перед укладкой обязательно нужно замачивать на 4–5 часов.
Первый ряд экрана обязательно выкладывается сплошным. Рекомендуется начинать со «щёчек» — мест, примыкающих к горловине топки. Так достаточно легко выйти на нужное значение зазора между экраном и корпусом печки, который в оптимальном варианте составляет 40–60 мм. Возможно, потребуется подрезка камней, её величину вы также определите на этапе примерки.
Когда перпендикулярно горловине топки уложены один-два кирпича с каждой стороны, поперёк им выкладываются стенки экрана. Начинать следует с лицевой части печи, делая небольшой выступ над щёчками. При устройстве выносной топки торцы стенок экрана выкладывают заподлицо с плоскостью стены или с небольшим выступом.
Чтобы кладка выглядела красиво, следует сразу нормировать толщину швов. Для кирпичной облицовки печи оптимальным значением будет 6–8 мм. Самый простой способ выровнять швы — укладывать по краям ряда два калиброванных прутка нужной толщины, сразу формируя галтельную расшивку. Важно лишь, чтобы перед извлечением прутков шов успел устояться около 15 минут.
Начиная со второго ряда, можно формировать пропуски для вентиляции. Если вы выбрали перевязку в треть длины, чтобы оставить в кладке оконце достаточно отрезать половинный добор и уложить его вместо целого кирпича — так вертикальный шов гарантированно не образуется над отверстием.
После того как стенки экрана выложены, выполняется закладка передней части. В зависимости от массивности горловины топки, кирпич можно укладывать как непосредственно на неё, так и на перекладину из стального уголка. Предварительно нужно подмостить горловину снизу, здесь может быть удобно поставить кирпич на ребро.
Глухой и открытый кожух
Нужно понимать теплофизику работы каменки, учитывать её мощность и особенности конструкции. Слишком маленький зазор приводит к перегреву из-за недостаточной конвекции, металл быстро устаёт, кладка разрушается от циклического перегрева. Зазор более 70 мм малоэффективен: теплового излучения будет недостаточно для прогрева экрана, и он лишится аккумулирующего эффекта.
Также важно, собираетесь ли вы оставлять зазор между печью и экраном открытым. В свободном пространстве будет создаваться достаточно мощный конвекционный поток, что хорошо, когда парилка имеет высокий потолок и значительный объём.
В последнем случае экран должен на 1–2 ряда выкладываться выше корпуса печи. Также не забывайте о нежелательности перегрева: если при открытом зазоре достаточно двух бойниц на одну сторону печи просто для забора воздуха, то закрытый экран должен быть более продуваемым. Рекомендуется делать по 2–3 ряда отверстий на разной высоте.
Расшивка, очистка
После завершения кладки экран нужно оставить сохнуть в течение недели. В это время печь можно слабо протапливать до очень слабого нагрева боковых стенок, не более. Когда глина в растворе окончательно отпустит влагу, экран можно считать завершённым и приступать к банным процедурам.
Однако внешний вид такого экрана невзрачен, поэтому с первых суток высыхания кладку моют и расшивают. Имеется два основных варианта приведения кирпичного кожуха в эстетически приемлемый вид.
Второй вариант — использовать расшивочный нож и рейку на следующий день после завершения кладки. Когда швы подведены, им дают укрепиться несколько суток и затем отчищают остатки раствора с кирпича металлической щёткой, либо шлифуют выступающие камни. Оба варианта выглядят эффектно при тонировании швов в цвет от песочно-белого до графитового.
рмнт.ру
Обкладка железной банной печи кирпичом своими руками
Металлическая печь – это и не очень красиво, и не совсем безопасно, так как чугун не просто быстро нагревается, но буквально раскаляется. Причем после стремительного нагрева происходит такое же стремительное остывание.
Но эти недостатки несложно исправить посредством обкладки кирпичом. Облицованная кирпичом конструкция смотрится не хуже полностью кирпичной каменки, а для ее сооружения нужны минимальные навыки.
Вариации на тему огнеупорного кирпича
Для обкладки банной печи — самодельной или готовой покупной Гефест и других производителей – обычный строительный кирпич не годится. Облицовочный материал должен обладать высокими огнеупорными характеристиками. Различают несколько типов огнеупорного кирпича в зависимости от того, какое сырье было использовано для его производства.
- Шамотный кирпич. Производится из шамотной глины с добавками в виде крупнозернистого кварцевого песка, графитового порошка или кокса. Благодаря этим примесям регулируется степень огнеупорности материала, а также другие его свойства. Может использоваться как для обкладки бытовых, так и промышленных печей, однако в промышленных целях используется материал с предельной огнеупорностью (+1750 градусов). Однако используется не так часто в бытовом строительстве печей, так как цена на продукцию довольно высока.
- Динасовый кирпич. Материал, по сути, является кремнеземом, так как изготавливается из кремнесодержащего порошка, который разводится в известковом молоке.
Если сравнивать с шамотным, динасовый кирпич отличается более высокой механической прочностью и огнеупорностью. Но эти достоинства нивелируются его главным недостатком – неустойчивость к температурным колебаниям. В связи с этим выложить таким материалом печь в бане – не самая удачная идея. Он больше подходит для промышленных сооружений, в которых поддерживается постоянная высокая температура.
- Тальковый кирпич. Неплохая огнеупорность и приятный внешний вид – вот козыри этого материала. Он производится из талькового сланца (природный материал) путем распиливания натурального камня на ровные кирпичики. Огнеупорность материала недостаточно высока, чтобы выкладывать из него печи, однако для облицовки он подходит идеально.
- Клинкерный кирпич. Подходит для обкладки только в том случае, если облицовка не примыкает вплотную к раскаленному железу.
Обратите внимание, что огнеупорная продукция может быть как гладкой, так и фасонной. Фасонные изделия подойдут тем, кто хочет придать каменке еще большую эстетичность.
Не экономьте на материале, покупая обычный глиняный кирпич. Подобная облицовка прослужит совсем недолго и быстро потрескается и начнет крошиться.
Нюансы, которые надо знать, приступая к облицовке
В целом, кладка кирпича для облицовки в плане технологии не отличается от кладки печных стен. Однако решив обложить чугунную или железную печь кирпичом, обратите внимание на важные моменты, перечисленные ниже.
- Каждый 4-й ряд облицовочной кладки рекомендуется армировать проволокой или стальной полосой. Топочный проем (в том числе проем выносной топки) армируется уголком из металла.
- В процессе облицовки своими руками вам понадобится теплоизолятор. В качестве него можно использовать асбестовый или базальтовый картон.
- Пересмотрите весь купленный кирпич на предмет дефектов (сколов, трещин и т.д.). Не поленитесь разложить материал на полу, подгоняя кирпичик к кирпичику так, чтобы тычки соприкасались с минимально возможным зазором.
Соблюдайте этот же порядок, когда будете класть кирпичи на раствор.
- Раствор для кладки должен соответствовать выбранному типу кирпича. Однако здесь ломать голову не придется. Обычно при покупке стройматериала вам сразу же предложат и сухую смесь, которую нужно только развести по инструкции водой.
- Следите за толщиной швов, не делайте их слишком широкими. Чем тоньше будут швы, тем лучшей теплопроводностью будет обладать облицовка.
- Обязательно проверяйте вертикальность углов отвесом, а также горизонтальность рядов уровнем.
Фундамент или пол – что лучше и надежнее?
Важно, чтобы кирпичная кладка опиралась на прочное основание, поэтому прежде чем начать работы, нужно оценить несущую способность пола. Рассчитайте массу запланированной кладки. Для этого умножьте количество рядов кирпичного экрана на количество кирпичей в каждом из них, а затем еще и на массу одного кирпичика.
Если масса менее 700 кг, вполне можно обойтись без фундамента, но при этом провести меры по усилению лаг. Необходимо проложить дополнительные лаги, скрепив их каркасом с основными. Затем следует обустроить негорючее основание, в качестве которого может быть использован лист металла (поверх слоя теплоизоляции), два ряда кирпичной кладки (кладется непосредственно на деревянный пол), керамическая жаростойкая плитка или искусственный камень.
Но если же вы сомневаетесь в прочности лаг, лучше изготовьте отдельный фундамент под каменку. Размер фундамента должен учитывать площадь самой печи, толщину облицовочной кладки, а также зазор между металлом и кирпичом (около 3-5 см), а также включать дополнительные 15-20 см к габаритам печного экрана. При увеличении ширины зазора замедляется прогрев облицовочной кладки.
Если решение сделать обкладку металлической печи пришло гораздо позже, чем сама печь была установлена, причем установлена она была БЕЗ фундамента, используйте пустотелый кирпич. Он быстро греется, не слишком долго держит тепло. Но зато весит он гораздо меньше, а это при отсутствии фундамента важный аргумент в его пользу.
Однако лучше все-таки разобрать пол и вырыть котлован по глубине идентичный глубине закладки фундамента самой бани. При этом основание под печь не должно быть связано с фундаментом банной постройки и располагаться от него на расстоянии минимум 5 см (это расстояние заполняется теплоизоляционным материалом). Высота основания под печь должна быть ниже уровня пола примерно на 10-15 см.
После заливки фундамента и 30-дневного периода его просыхания уложите на него поэтапно следующие материалы: два слоя влагоизолирующего материала (например, рубероида), два кирпичных ряда на глино-цементном растворе.
Технология кладки кирпичного экрана
Опытные печники советуют обкладывать металлическую печь в полкирпича. Перегородку можно сделать, конечно, и в целый кирпич, но, во-первых, он слишком долго прогревается, а во-вторых, обязательно требует фундамента.
Также допускается делать экран в разрядку, то есть со своеобразными окошками, или в четверть кирпича. Это обеспечивает очень быстрый нагрев банного помещения, но при этом придется мириться с мощным инфракрасным излучением от металла.
Чтобы ускорить прогрев парилки, но при этом обустроить сплошной экран, можно оставить в кладке окошки, которые впоследствии закрыть кирпичом (без раствора) или вставить в них печные дверцы. Пока помещение прогревается, эти элементы можно достать, а затем снова поставить на место, когда придет время париться.
Если вы кладете сплошной экран, обязательно оставьте в 1-м и 2-м ряду по два отверстия примерно по 12 см (продухи) с каждой стороны, которые обеспечивают ускоренную конвекцию и обогрев. Эти же отверстия нужно повторить в верхних рядах. Если ваша каменка достаточно мощная, защитите эти отверстия литыми печными дверцами. Это поможет вам с легкостью регулировать температуру в бане.
Верх печи можно оставить открытым, так как тепловое излучение смягчают камни. Но если температура для вас слишком высока, положите на готовый экран металлическую сетку из толстой проволоки с маленькой ячейкой, а затем наверх уложите камни для бани. Это снизит жар, но все-таки добавит проблем при обслуживании печной конструкции.
Если ваша каменка имеет круглую форму, технология обкладки будет такая же. Однако вентиляционные окошки нужно располагать симметрично друг другу и на одинаковом расстоянии. Сложность в этом случае будет заключаться лишь в том, что нужно особо внимательно следить за расстоянием между кладкой и печью.
При облицовке буржуйки также не должно возникнуть проблем. Процесс усложнится разве что тем, что придется дополнительно выполнить проемы под поддувальную и топочную дверцы, а затем перекрыть проемы 2-мя отрезками стальных уголков, расположив их внутри и снаружи кладки.
Угольная печь своими руками — Tim Tinker
Этот сайт содержит партнерские ссылки. Таким образом, я буду зарабатывать на соответствующих покупках без каких-либо дополнительных затрат для вас. Это помогает мне поддерживать этот веб-сайт, так что спасибо за вашу поддержку.
Самодельная угольная печь, которая может самостоятельно производить древесный уголь из древесных отходов, предварительно обжигая и полностью обжигая самодельную керамику.
Я не возражаю против небольшой двусмысленности в названии. Я могу быть краток и задать читателю вопрос: это устройство, которое производит древесный уголь или использует древесный уголь? В данном случае это и то, и другое, и оно может даже приготовить мне ужин или закоптить моих угрей!
Когда она в конце концов достигла точки плавления болотной обыкновенной студенческой глины, я решил назвать ее моей печью Навуходоносора, согласно библейскому рассказу, где Навуходоносор якобы сделал печь «……..в семь раз больше, чем обычно отапливать……». Не позволяйте фактам или физике мешать хорошей истории, но в моем случае печь выжила (и нуждалась в небольшом огнеупорном ремонте), и я достиг своей цели плавления белой глины!
Мотылинка Старшая
Знакомство с угольной печью своими руками
Этот пост находится в разработке.
Я играю с огнём и по возможности предпочитаю использовать отходы упавших деревьев для своей игры с огнем. Вероятно, я вырастил слишком много деревьев, и теперь у меня есть лишняя древесина, которая не нужна для обогрева моего дома, иначе она сгорела бы в загоне.
Древесный уголь из такой древесины при обдуве принудительным воздухом достигает самых высоких температур горения этого скромного топлива для обжига керамических изделий своими руками.
Я надеялся сделать печь, которую можно было бы использовать для получения древесного угля из древесных отходов. Это означало бы, что тепло от его пиролитического превращения в древесный уголь может производить умеренные температуры, которые можно использовать для других целей, таких как длительная и устойчивая подготовка керамики к их окончательному обжигу.
Полезными побочными продуктами могут быть другие процессы с использованием тепла, такие как плавление металлов, медленное приготовление пищи и даже копчение мяса. Дополнительный начальный бонус можно было бы получить, если сделать печь из огнеупорной смеси, которая по сути представляет собой почву. «Будет забавно посмотреть, сможет ли печь поджечь собственные стены, как в этом маленьком видео?»
Тестирование прототипа. Я сделал небольшой прототип печи из четырех кирпичей, земли и листа металла, и во время фазы устойчивого горения древесного угля температура печи достигла 1250°C. У него было много утечек, плохая изоляция, обеспечиваемая верхней крышкой из листового металла, и ограниченный приток воздуха, подаваемый небольшим вентилятором USB. Я предположил, что смогу достичь гораздо более высоких температур с помощью хорошо спроектированной печи с минимальными утечками, хорошей изоляцией и нагнетанием воздуха мощного пылесоса. Вот небольшое видео прототипа в действии.
Миниатюрный прототип печи из кирпича и огнемета USB. Он очень примитивен, но может нагреваться до 1250°C, когда он закрыт крышкой из листового металла.
Испытание футеровки печи. Во время испытаний прототипа печи я также поместил образец предложенной мной самодельной теплоизоляционной футеровки печи, чтобы посмотреть, как она справляется с суровыми условиями этой адской дыры. Это была смесь перлита, мелкоизмельченного суглинка (без глины) и силиката натрия. Подробнее читайте в моем посте о огнеупорах из силиката натрия своими руками.
Он уцелел, немного треснул, но в него впилась сетка из птичьей проволоки. Он стал очень легким и приобрел стеклянную текстуру. Может потребоваться еще одно окончательное покрытие, чтобы уменьшить остекление, если печь достигает значительно более высоких температур. Я нанес тальк на каждую сторону тестового образца. Похоже, это предотвратило чрезмерное застекление, которое я наблюдал в предыдущих тестах. Это достигается за счет повышения температуры плавления поверхности.
Экспериментальная керамическая футеровка печи после сушки на воздухе и затем в печи до 220°С. Он состоит из перлита, тонкоизмельченного суглинка (без глины, я называю его постямным грунтом) и силиката натрия.
Отверждение углекислым газом. Я часто использую силикат натрия для изготовления огнеупоров, а отверждение изделий перед полным обжигом требует умеренных температур в диапазоне ~200-300°C для удаления химически связанной воды.
Также высокая концентрация двуокиси углерода в воздухе ускоряет превращение силиката обратно в двуокись кремния (при подготовке к превращению в стеклокерамику при высоких температурах). Такое тепло и богатые пары углекислого газа образуются при пиролизе древесины в древесный уголь.
Впоследствии я обнаружил, что температура в печи может легко достигать 200-300°С в верхней части топочной камеры во время сжигания древесины с естественной тягой для производства древесного угля. Это должно обеспечить устойчивые условия сушки/отверждения перед высокотемпературным обжигом древесного угля.
Всепогодный и мобильный. Было бы лучше, если бы печь была защищена от непогоды, чтобы ее можно было безопасно хранить снаружи, возможно, в шапке от дождя. Мобильность означает, что его можно перемещать, если он мешает, или его можно переместить в место, наиболее подходящее для его потенциального использования (например, угольщик для копчения или тихий курильщик угря). Следовательно, прочное круглое бетонное основание казалось хорошей отправной точкой для формирования бочкообразной огнеупорной стены печи.
Основание угольной печи
Основание из портландцемента. Я изготовил цилиндрический профиль из листового металла (нижний и без верха), чтобы отлить в него основание печи. Я приварил колено для подачи воздуха диаметром ~40 мм, которое отлил в середину основания. Внутренний выход трубы был направлен вверх к зазору с небольшим сменным фитингом для решетки, который предотвратил бы падение больших кусков угля в трубу.
Планировалось использовать этот воздухозаборник в качестве устройства с ограниченным доступом воздуха для производства древесного угля и отверждения углекислым газом с использованием естественной тяги печной трубы. В качестве альтернативы, его можно использовать для небольшой принудительной подачи воздуха из небольшого пожарного вентилятора USB (как показано на некоторых фотографиях ниже, где огнеупорная штукатурка была отверждена пламенем и углекислым газом). Наконец, для окончательного высокотемпературного сплавления керамики он мог бы нагнетать воздух из пылесоса, работающего от сети. «Пылесосы, которые выбрасывают повсюду, потому что они стали излишними благодаря революции стиля Дайсона».
Основание печи выполнено из простого песка и портландцементной смеси.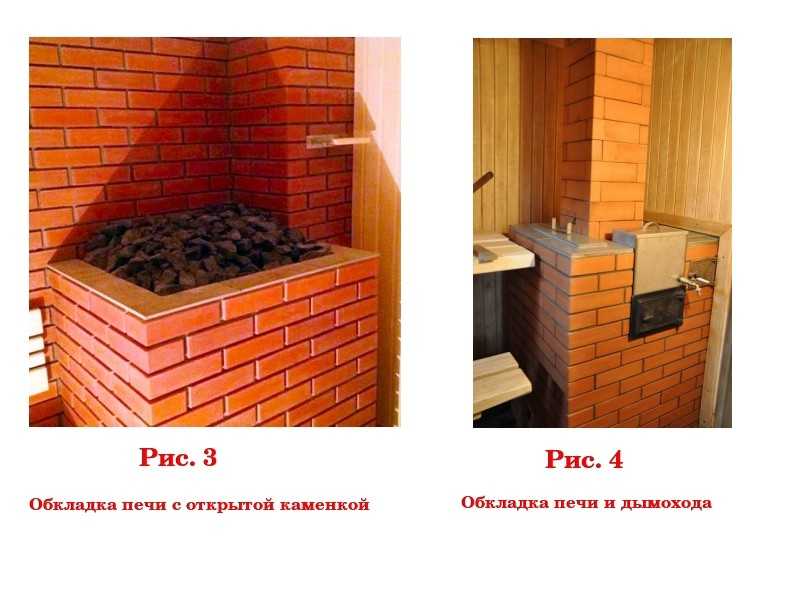
Нижняя часть отливки была выполнена из смеси портландцемента и песка с добавлением армирующей проволоки и легкой сетки для защиты от катаклизмического растрескивания основания. Я не ожидаю, что он станет настолько горячим, что портландцемент разрушится.
Высокотемпературный изоляционный цемент. Затем я добавил щедрый слой перлита, смешанного с высокотемпературным цементом и водой. «Высокая доля перлита в цементе делает смесь странной, поскольку перлит просто плавает в цементном порошке, как рисовые пузыри и сахар, пока не будет добавлено небольшое количество воды». Он хорошо наливался и утрамбовывался, и его можно было обрабатывать, как обычный цемент, с щедрой трамбовкой. Гранулы перлита ведут себя как мелкие агрегаты. Я также оставил возможность добавить дополнительный горячий рендер лица, если это когда-нибудь понадобится. Тем не менее, мой опыт работы с очень горячими воздухонагревателями показывает, что тепло не уходит вниз через вездесущий слой золы. Время покажет.
Стенка печи. Не знаю, как назвать, но стена сойдет. Это будет изолированный корпус, куда будет поступать древесное топливо, формироваться древесный уголь, а керамические творения будут купаться в пламени древесного газа, а затем излучаться интенсивным теплом от сжигания древесного угля с принудительной подачей воздуха.
Боковой порт для печной трубы. Я надеюсь сделать отверстие для дымохода, чтобы его можно было использовать для создания естественной тяги для медленного горения, когда не требуются самые высокие температуры. Это означало бы, что купол можно закрыть простой круглой огнеупорной крышкой. В качестве альтернативы можно нагреть сверху кастрюлю для медленного приготовления или коптильню.
Стенка печи. Я сделал стену достаточно высокой, в виде плавно сужающейся конической формы с большим отверстием наверху. Емкость намного больше, чем все, что я могу выстрелить. Тем не менее, я надеялся, что его можно будет загрузить большим количеством необработанной древесины, которая может пиролизоваться в древесный уголь и со временем падать вниз, чтобы пополнить древесный уголь, который будет ближе всего к соплу воздушной струи.
Внутренняя форма купола была изготовлена из 22-литровой бочки из-под растительного масла, которую я разрезал в четырех местах. Я снова собрал барабан, чтобы он был конусообразным и его можно было легко извлечь после того, как купол был оштукатурен изолирующим огнеупором. Пластиковый лист был обернут вокруг конуса, чтобы при необходимости он мог легко отделяться от рендера.
Фундамент угольной печи с формообразующим конусом для стены купола устанавливается на место с укладкой вокруг него слоя армирующей сетки. Стена купола угольной печи. Самый внутренний слой купола представляет собой самодельный огнеупор, сделанный из суглинка (в основном не содержащего глины), силиката натрия и перлита, чтобы сделать его изолирующим и довольно легким (как описано выше). Слой легкой оцинкованной проволоки, мы надеемся, защитит от катастрофического обрушения.
«Как только я закончил смешивать первую партию огнеупорной штукатурки, как всегда пошел дождь. Поэтому я быстро опробовал портативность угольной печи, поставив ее на тележку для мешков, и ее было восхитительно легко перемещать под навесом. .»
Основание угольной печи с первым огнеупорным и изоляционным слоем, нанесенным на каркас временной стены купола. Штукатурка наносится очень легко, но начинает оседать при толщине более 15-20 мм. Я решил, что для хорошей изоляции потребуется второй слой той же огнеупорной смеси. Это также даст удобную возможность добавить второй слой армирующей сетки в виде спирали из птичьей проволоки. В любом случае потребуется значительное количество времени на сушку/отверждение для набора прочности перед следующей обработкой. Или будет?
Когда снимать куполообразную форму?
Я могу снять формовочную форму после высыхания штукатурки, но тогда она может дать усадку и сильно треснуть или застрять в форме. С другой стороны, если бы я удалил форму, пока рендер был «зеленым», я бы избежал усадки и застрял на сценариях. Раннее удаление плесени значительно увеличит скорость высыхания, а силикатная штукатурка способна заживать, пока она зеленая. Я взял плоскодонку и удалил форму, пока рендер был в этом деликатно твердом зеленом состоянии. «Похоже, эта авантюра окупилась»
Тонкая стена купола печи ненадежно держится вместе с высокотемпературной штукатуркой с высоким содержанием силиката почвы в ее зеленом состоянии после удаления внутренней формы. У меня возникло искушение попытаться заполнить небольшие пустоты, оставленные в рендере выпуклостями в пластиковой пленке. Однако при этом я ткнул пальцем в стену и на данном этапе отказался от этой идеи как от плохой.
Немедленно стрелять, чтобы ускорить лечение или нет? Отказавшись от косметического ремонта, я почувствовал, что удача еще со мной. Я решил ускорить отверждение зеленого рендера, зажег внутри него небольшой огонь. «В конце концов, это то, для чего это нужно!» Такой нагрев огнем ускоряет отверждение за счет его высыхания и значительного увеличения концентрации двуокиси углерода, которая участвует в превращении силиката в форму двуокиси кремния при подготовке к высокотемпературному превращению в стекловидный кремнезем.
Поджигание огнеупорной штукатурки стены противопожарного купола для ускорения высыхания/отверждения огнеупорного материала из силиката натрия. Это быстро сделает его намного прочнее, если вы нанесете дополнительные слои стены купола. Установите еще больший огонь, чтобы быстро вылечить рендер огненного купола. Обжиг рендера достиг 550°C (максимальная температура по термометру) в верхней части купола, а в нижней зоне температура превышала 550°C. Эта температура в сочетании с высоким содержанием углекислого газа делала внутреннюю часть печи твердой и твердой. Вот небольшое видео обстрела.
Эти температуры означают, что это хорошее предварительное отверждение, которое делает штукатурку готовой к полному обжигу керамики. «Это небольшое видео показывает обжиг рендера и его трансформацию в хард-финиш. Это всего лишь концепция керамики, ее настоящее рождение происходит при гораздо более высокой температуре, когда она становится стекловидной субстанцией. Это произойдет, пока печь будет введена в эксплуатацию.
Следующий внешний слой должен был состоять из смеси портландцемента и песка с перлитом. Однако я подумал, что для большей глубины изоляции необходим дополнительный слой силикатного перлита почвы. «В любом случае, это чертовски дешево!» Окончательные внешние слои портландцемента придадут дополнительную прочность и стойкость к истиранию, а внутренние слои будут хорошо защищены от нагревания.
Огнеупорная штукатурка, покрывающая горячую поверхность печи
Думаю, я немного поторопился с обжигом первого огнеупорного слоя, пока он был «сырым» или не отвержденным всухую. «Конечно, у него не было такой жесткой текстуры безе, как на тестовом образце, показанном выше». Он был немного рыхлым и недостаточно прочным для загрузки грубых дров. Поэтому я сделал мягкую мелкую штукатурку из талька (детская присыпка) и силиката натрия (40 г силиката: 40 г талька: 80 г воды). Она была преднамеренно насыщена силикатом и довольно «жидкая», и я очень аккуратно нанес штукатурку кистью на потрескавшуюся и рассыпчатую поверхность. Влага и растворенный силикат быстро впитывались в первоначальную поверхность, и тальк начал заполнять трещины и отверстия. Поверхность, обработанная таким образом, быстро становилась очень стабильной, а штукатурка быстро затвердевала.
Я сделал больше штукатурки и сразу же смог нанести второй слой, в результате чего получилась гладкая, прочная и плотная поверхность. «На этот раз я бы не стал спешить с обжигом керамического покрытия».
Печь на древесном угле, на довольно тонкую и рассыпчатую изолирующую огнеупорную стенку была нанесена тонкая горячая штукатурка из порошка талька/силиката натрия.
Еще одно огнеупорное покрытие горячей поверхности печи
Принимая во внимание улучшение поверхности талько-силикатной штукатурки, я подумал, что было бы неплохо нанести дополнительное более толстое покрытие горячей поверхности. У меня заканчивалась детская присыпка, поэтому я использовал немного гранатового порошка (отходы из поддона станка для гидроабразивной резки). «Из опыта я знал, что он может сделать огнеупор твердым, как камень для заточки ножей». Итак, огнеупорная смесь была такой (40 г силиката: 40 г талька: 400 г порошка граната: 100 г воды).
Это была очень густая смесь, которую я обильно нанесла кистью, чтобы полностью покрыть белый цвет тальковой штукатурки. Эта смесь застряла в щетине кисти, так как жидкая фаза втягивалась в поверхность во время чистки. Поэтому я использовал две заливки ~100 г воды во второй кастрюле, чтобы смягчить и удалить рендер с кисти. Постепенно эти дополнительные горшки с водой стали похожи на рендер, и я использовал их, чтобы смочить или загрунтовать поверхность, прежде чем быстро нанести окончательный рендер. Таким образом, ни один компонент рендера не был потрачен впустую, все ушло на горячую поверхность или на нее.
Внешняя поверхность угольной печи
Чтобы сделать печь снаружи прочной, я нанес толстый слой штукатурки из песка и портландцемента. Этот рендер был нанесен через слой тонкой оцинкованной проволоки для птиц. Последней штукатуркой будет белый цемент с добавлением гидроизоляции «влажного слоя». «Этот последний рендер был использован только ради красоты и тщеславия, а также потому, что у меня остались остатки в мастерской, и он заставляет уродливый цемент выглядеть великолепно, как дома на греческих островах».
Угольная печь покрыта двумя слоями портландцементной штукатурки снаружи после добавления цилиндра сетки из птичьей проволоки.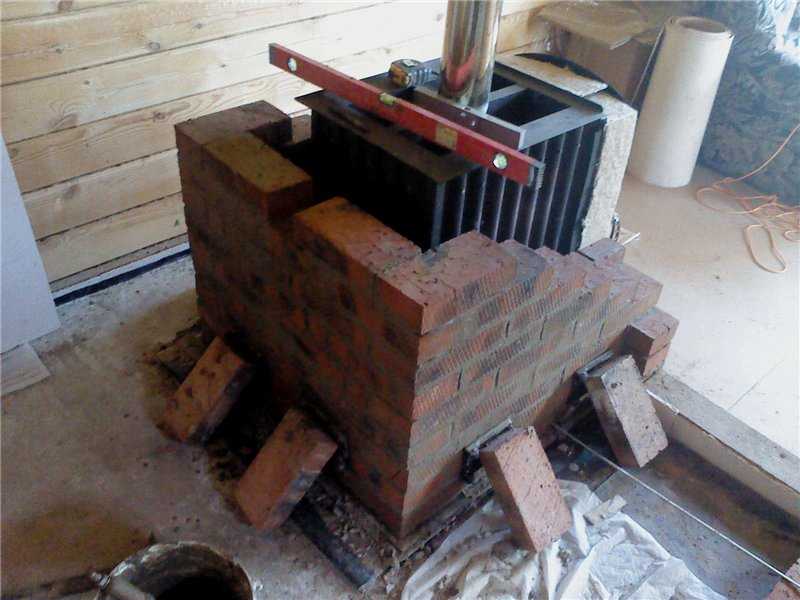
Кто забыл встроить порты для датчика термопары печи?
Рендеринг прошел так быстро, что я забыл добавить порты для термопар. Я сделал три маленькие трубки из нержавеющей стали, которые собирался вставить в стену печи, чтобы можно было вставить дешевый термопарный зонд для контроля температуры. Один наверху, где я мог бы готовить и курить, один посередине в зоне пиролиза и один в зоне высокотемпературного сжигания древесного угля. Неважно, этот рефрактор можно очень легко просверлить после затвердевания, поэтому я все еще могу добавить порты и продолжить визуализацию вокруг них.
Вот фотография модернизированных портов для термопар. Просверлив отверстия с помощью сверла по каменной кладке, я вставил в стену портовые трубки из нержавеющей стали для термопары с помощью моей чудодейственной алюминиевой фольги и расширяющегося огнеупора из силиката натрия. «Это волшебная штука, поскольку она пузырится, пенится и расширяется сама по себе, когда ее помещают в маленькое место, и становится огнеупорным огнеупором, который просто смеется над огнем».
Функциональные температуры для изготовления огнеупоров
В конце концов я остановился только на двух портах контроля температуры. Я обнаружил, что температура в печи достигала 200-300°С в верхней части с естественной тягой, где новые огнеупоры можно было аккуратно высушить и затвердеть, одновременно готовя древесный уголь для окончательного обжига. Зона в месте расположения среднего порта (показана на фото выше) достигла температуры около 1050С, что согласно вышеприведенному посту Апровечо должно обеспечить адекватный обжиг печных огнеупоров. Я отказался от идеи порта внизу в слое древесного угля, так как ожидал, что температура выйдет далеко за пределы 1300C для моей термопары K-типа.
На приведенных ниже фотографиях показаны керамические пробные шайбы, обожженные в печи. Шайбы практически не видны при самой высокой температуре на первом фото, сразу после поднятия крышки топки. Когда печь немного остынет, шайбы станут видны.
Посмотрев на эту печную адскую дыру, я думаю, пора подумать о наших храбрых братьях и сестрах Украины:
Удивительно, до злости и досады, Когда вы обманываете свою молодость, чтобы вторгнуться в другую нацию, Армия Голиафов погублена собственной воинственностью, Против стойкой защиты Родины Давида, Кроме того, помните, во что обойдется вашей стране возмещение ущерба за войну!
Кто забыл отверстие для удаления золы?
Для человека, который так много играет с огнем, я не должен был бы удивиться, обнаружив, что удалить пепел из такой печи довольно сложно. Возможно, со временем я вырежу зольник и сделаю для него керамическую заглушку.
Раньше накопление золы происходило, когда я использовал печь с естественной тягой или с крошечным USB-огнедувкой. К счастью, когда я разжег печь с помощью бластера с принудительной подачей воздуха, сделанного из старого «двойного» пылесоса Electrolux. «Попробуй сделать это со своим Дайсоном!» Взрыв был настолько сильным, что не нужно было удалять значительного количества пепла, поскольку он просто оставил небольшой вулканический конус пепла вокруг входного отверстия для воздуха. «Хорошее изоляционное покрытие для следующего использования». Вот небольшое видео работы доменной печи на полной мощности.
Заключение
Этот самодельный огнеупорный проект показал, что печь на древесном угле можно сделать из почвы и силиката натрия. При наличии терпения его можно использовать для самовоспламенения, чтобы он стал изолирующим и жаростойким огнеупором. Затем он сможет удобно вулканизировать и обжигать другие огнеупорные изделия при высоких температурах, используя древесные отходы от упавших веток.
Тим
Приложение
После небольшого количества проб и ошибок мне удалось нагреть печь до устойчивой температуры, при которой можно обжечь «белую студенческую глину», чтобы она плавилась должным образом и даже начала плавиться и немного оседать. .
Предметы из бумажной глины, которые были обожжены в моей самой горячей печи Навуходоносора с полной загрузкой качественных дров.
Осмысление вкладышей дымохода
Многие дымоходы в старых домах служат очагом на каждом этаже с несколькими дымоходами, которые змеятся через выступы в каменной кладке. (Фото: Paul Rocheleau)
Большинство владельцев старых домов наслаждаются теплом каминов или отопительных печей, поэтому они знают, что важно регулярно осматривать и чистить работающий каменный дымоход. Национальная ассоциация противопожарной защиты (NFPA) рекомендует ежегодно проверять дымоходы, работающие на твердом топливе — дровах, угле или пеллетах, и очищать их по мере необходимости. Такое техническое обслуживание помогает обеспечить целостность конструкции, выявить дефекты, которые могут привести к попаданию смертоносных газов сгорания в жилые помещения, и предотвратить возгорание дымохода, вызванное накоплением креозота, естественного побочного продукта горения древесины.
Тем не менее, немногие домовладельцы, которые используют свои дымоходы только для вентиляции газовых или жидкотопливных печей и котлов, знают, что к ним также относятся техническое обслуживание и надлежащие условия. Это проблема, потому что побочные продукты сжигания газа и нефти так же коварны, как и продукты твердого топлива. Дымоходы — или, точнее, дымоходы внутри них — должны быть чистыми и прочными, чтобы безопасно отводить тепло и газы вверх и от верхней части дымохода, но эти побочные продукты сгорания также могут со временем повредить внутреннюю поверхность дымохода.
Допустим, вы проверили дымоход, и допустим, в отчете содержится рекомендация о том, что ваш дымоход необходимо заменить. Мы рассмотрим, что это значит, а также лучший способ решить проблему для вашего конкретного дымохода и дома.
Гибкие вкладыши, такие как этот гофрированный из нержавеющей стали, хорошо подходят для модернизации дымоходов со смещением или узкими размерами. (Фото: Поставка дымоходов/Американский институт безопасности дымоходов)
Линия на вкладышах
Одной из главных причин для замены футеровки каменного дымохода является то, что он изначально был построен неправильно, то есть без облицовки дымохода, материала, который обеспечивает гладкую, относительно бесшовную поверхность, а также изоляцию. Исторически сложилось так, что хорошо сложенные дымоходы заполнялись раствором для покрытия дымохода, а глиняная черепица была стандартной облицовкой с 1900-х годов. Тем не менее дымоходы без вкладышей по-прежнему очень распространены как в старых, так и в новых домах. Строители и установщики отопительного оборудования не всегда соблюдают рекомендуемые методы, а если и соблюдают, то не утруждают себя их соблюдением.
Если у вашего дымохода есть футеровка, другой причиной, по которой вам может потребоваться замена футеровки, является ее неисправность. Возраст и эксплуатация могут привести к появлению трещин в плитке, а дымовые газы в сочетании с дождем разрушат швы между кирпичами и камнями. Если преобладание доказательств указывает на перебазировку, у вас есть несколько вариантов для рассмотрения.
Вы можете 1) реконструировать дымоходы из глиняной плитки с новыми вкладышами из глиняной плитки, 2) укрепить дымоход и создать новые дымоходы с вкладышами из литого цемента или 3) переделать существующие дымоходы и проложить новые с металлическими вкладышами дымоходов. Каждый метод имеет свои преимущества, ограничения и проблемы. Подход, который вы в конечном итоге выберете, должен быть тем, который лучше всего подходит для проблем конкретного дымохода и устройств, вентилируемых через него.
Глиняные плиты для дымоходов представляют собой прямоугольные или круглые керамические блоки высотой 24″, которые укладываются друг на друга со швами, залитыми раствором, чтобы получилась облицовка. Несмотря на высокую прочность, плитка может треснуть из-за возраста или повреждения, а ее вес и жесткость затрудняют ее модернизацию. (Иллюстрация: Рэнди Суитцер)
Вкладыши из глиняной плитки
Дымоходы из глиняной плитки являются традиционным фаворитом. Дымоходные плиты практически невосприимчивы к теплу и коррозионным побочным продуктам сжигания любого топлива. При правильной отделке швов огнеупорным раствором срок службы дымохода из глиняной черепицы может составлять 50 и более лет при минимальном обслуживании, кроме регулярной очистки.
Но квадратные и прямоугольные дымоходы не самая эффективная форма для отвода дыма. По своей природе дым поднимается вверх по дымоходу по спирали, оставляя несоответствующие воздушные пространства по краям. В лучшем случае эти воздушные пространства просто занимают дополнительное место в дымоходе, которое может понадобиться для дополнительных дымоходов; в худшем — уменьшают тягу. Круглые дымоходы намного эффективнее.
Глиняная облицовочная плитка относительно недорогая – около 10 долларов за типичную единицу высотой 24 фута. Но то, что вы сэкономите на материалах, скорее всего, превысит затраты на монтажные работы. Глиняные вкладыши трудно модернизировать в существующем дымоходе, особенно если он не прямой. Даже для прямого участка необходимо пробивать стены дымохода через каждые несколько вертикальных футов, чтобы получить доступ для удаления старой плитки дымохода и укладки новой плитки.
Для дымоходов со смещением (изгибом) дымоходные плиты необходимо обрезать под точным углом для получения приемлемых швов. В некоторых районах трудно найти человека, обладающего навыками для такого рода установки, и это определенно не работа владельца-реставратора.
Монолитные вкладыши представляют собой запатентованные процессы, при которых раствор закачивается внутрь дымохода для формирования нового дымохода. В одном методе, показанном вверху, для формирования дымохода используется надувная камера. Альтернативный процесс, показанный внизу, заключается в том, что остроконечный раструб поднимается вверх по дымоходу, образуя дымоход. (Иллюстрация: Рэнди Свейцер)
Монолитные вкладыши
Если новая глиняная черепица невозможна, можно создать новый дымоход в поврежденном каменном дымоходе, используя один из нескольких способов заливки цемента. Вообще говоря, этот подход предлагает все преимущества глиняных дымоходов плюс еще несколько. Монолитные дымоходы практически невосприимчивы к вредному воздействию тепла, кислот и конденсата, независимо от типа сжигаемого топлива. Температура внутри монолитных дымоходов обычно высока из-за их изоляционных свойств, поэтому они горят чище и уменьшают накопление креозота.
Ожидайте, что дымоходы из литого цемента прослужат не меньше, чем глиняная плитка — 50 или более лет. Некоторые компании утверждают, что монолитные дымоходы могут стабилизировать ненадежные глиняные дымоходы и дымоходы, поскольку они заливаются либо внутри существующего дымохода, либо в стенках дымохода.
Хотя процесс литья на месте может быть менее трудоемким и инвазивным, чем реконструкция глиняных дымоходов, существует ряд различных запатентованных методов литья. В некоторых проектах стоимость требуемой рабочей силы может быть равна или превышать стоимость замены глиняной плитки. Как всегда, наилучший подход зависит от условий, характерных для конкретной работы. Ни в коем случае заливка дымохода на месте не является самостоятельной работой. Материалы и оборудование для заливки дымоходов на месте поставляются различными производителями дистрибьюторам/техникам, выполняющим монтаж.
Если в проблемном дымоходе есть один или несколько глиняных дымоходов, установщик определит, можно ли оставить плитку на месте или ее нужно удалить. Определяющие факторы включают структурное состояние существующего дымохода и дымохода, а также необходимое пространство в зависимости от размера и количества необходимых дымоходов.
В первом из двух распространенных методов литья дымоходов, продаваемых под различными торговыми марками Golden Flue, Solid/Flue Chimney Systems и Supaflu Chimney Systems, замена футеровки начинается с предварительной очистки дымохода.
Затем техники вставляют одну или несколько надувных камер от выхода отопительного прибора до верха дымохода. Затем они устанавливают опалубку в основании дымохода и размещают распорки вокруг пузырей, чтобы отделить их от дымохода. В этот момент они закачивают в дымоход грязеподобную смесь легкого огнеупорного цемента и изоляционного заполнителя, пока она не заполнится до верха дымохода. После затвердевания цемента баллоны сдуваются, опалубка снимается и выполняются все необходимые отделочные работы. Результат: один или несколько конструктивно жестких, гладких, непрерывных дымоходов с хорошей изоляцией.
При втором методе литья дымоходов, продаваемом под торговыми марками Ahrens Chimney Systems и Guardian Chimney Systems, техники медленно закачивают футеровочный материал консистенции глины в дымоход, в то время как они втягивают вибрирующий колокол (заостренный формовочный инструмент) вверх через цемент. для формирования дымохода. В методе Аренса есть второй этап, когда технический специалист распыляет верхний слой суспензии на канал дымохода, чтобы обеспечить более гладкую, невпитывающую поверхность, которая, как говорят, увеличивает тягу и облегчает очистку. Оба метода литья используются в Европе более 70 лет, а в США — более 30 лет9.0003
Вкладыши дымоходов из нержавеющей стали бывают жестких и гибких форм, различных конструкций и сплавов, что делает их одними из самых универсальных вкладышей. Одним из преимуществ гибких металлических вкладышей является их способность приспосабливаться к смещениям и другим «сюрпризам» старых дымоходов. (Иллюстрация: Рэнди Суитцер)
Металлические дымоходы
Прагматики, в том числе многие установщики и эксперты по противопожарной защите, с которыми мы консультировались, обычно предпочитают дымоходы из нержавеющей стали. Как правило, для их установки требуется меньше труда, чем для других типов вкладышей, и они легко доступны в различных типах и размерах для всех распространенных отопительных приборов, включая камины и дровяные печи. Установленный профессионалом металлический вкладыш стоит около 100 долларов за фут.
Проблема реставраторов старых домов заключается в том, что существует так много различных типов и размеров металлических дымоходов, что бывает трудно выбрать, какой из них лучше всего подходит для данного применения. Хорошей новостью является то, что большинство широко используемых вкладышей дымохода доступны в комплекте с изоляционными накладками и фитингами для подключения к каминам, печам, печам и котлам.
Вкладыши дымоходов из нержавеющей стали бывают жесткими и гибкими. Жесткие дымоходы доступны в диаметрах от 3 до 10, а гибкие гофрированные металлические трубы имеют диаметр от 2 до 10. Жесткие дымоходы не следует путать с дымоходами с двойными или тройными стенками, которые предназначены для незакрытых дымоходов и не должны использоваться в качестве дымоходов. Жесткие вкладыши лучше всего подходят только для прямых дымоходов без выступов и изгибов.
Существует дискуссия о том, легче ли чистить жесткие вкладыши дымоходов, чем гибкие вкладыши с гофрированной поверхностью. Наш самый надежный эксперт говорит, что гибкие вкладыши, как правило, собирают меньше креозота, когда используются для вентиляции дровяных каминов и печей, потому что они изгибаются, расширяясь и сжимаясь при колебаниях температуры, в результате чего отложения ослабевают и отпадают.
Для вентиляции камина выберите диаметр, обеспечивающий вентиляционное отверстие, равное одной восьмой общей площади каминного отверстия. Для дровяных печей и других отопительных приборов следует обращаться к рекомендациям производителя относительно диаметра дымохода. Самым сложным аспектом выбора подходящей футеровки из нержавеющей стали является выбор правильного сплава в зависимости от типа сжигаемого топлива. Тщательный выбор предотвращает коррозию, которая является основной причиной преждевременного выхода из строя дымоходов из нержавеющей стали.
Также рекомендуется изолировать металлические дымоходы с помощью оберток или кожухов, специально предназначенных для этой цели. Изоляция особенно важна вокруг вентиляционных отверстий высокоэффективных обогревателей и печей, поскольку температура их дымовых газов обычно ниже, чем у обычных моделей.