Зарубежный опыт применения композитной арматуры 🌍
Мировой опыт применения
композитной стеклопластиковой арматуры
Показываем примеры использования композитных армирующих материалов за границей. Смотрите как применяется полимерная арматура в США, Канаде и Европе. В конце статьи видео-отзывы экспертов из США с переводом на русский язык в субтитрах.
За рубежом композитную арматуру обозначают аббревиатурой GFRP (Glass Fiber Reinforced Plastic Bar). Дословно переводится как «стекловолокно, усиленное пластиком».
Нет времени читать всю статью? Сохраните её в социальных сетях или отправьте себе в мессенджер!
Первый опыт применения стекловолокна датируется 1956-м годом в США. Массачусетский технологический институт несколько лет разрабатывал проект дома из полимерных материалов с применением стекловолокна. Он предназначался для одного из аттракционов парка «Диснейлэнд» в Калифорнии. Он прослужил 10 лет, пока его не решили заменить другой достопримечательностью и определить под снос.
Когда металлический шар-молот, предназначенный для сноса зданий, коснулся конструкции, он просто отскочил от неё, словно резиновый мячик. Здание пришлось разбирать вручную.
В последующие десятилетия было решено использовать полимерные композитные материалы для армирования бетонных конструкций. В разных странах (СССР, Япония, Канада и США) велись разработки и испытания инновационного продукта.
В Советском Союзе идея использования стеклянного волокна для армирования была впервые озвучена в 1941-м году. Об этом вы можете узнать из книги Николая Фролова «Стеклопластиковая арматура и стеклопластбетонные конструкции».
Интересный факт! В Канаде испытали мореходные судна, изготовленные с применением стекловолокна и отслужившие 60 лет. Результаты тестов показали, что существенного ухудшения прочности материалов за шесть десятилетий эксплуатации не произошло (по материалам ресурса http://www. frpdistributors.com/)
Некоторые примеры использования полимерной композитной арматуры из зарубежного опыта:
- Применение GFRP в Европе начато в Германии, она использовалась для постройки автодорожного моста в 1986-м году.
- В Японии еще до середины 90-х насчитывалось больше ста коммерческих проектов. Подробные рекомендации по проектированию и строительству с участием композитных материалов разработаны в Токио в 1997 году.
- В 1997-м году построен мост Headingley в канадской провинции Манитоба.
- При постройке моста Joffre Bridge в Квебеке (Канада) армированы напорные плиты, тротуар и дорожные заграждения. Мост открыт в 1997-м году, а в структуру арматуры были интегрированы волоконно-оптические датчики, чтобы дистанционно контролировать деформацию.
- В Британской Колумбии в 1998-м году построен винный завод.
- В 2000-х годах Китай стал самым крупным потребителем в Азии, используя стеклоарматуру в различных сферах строительства — от подземных работ до настилов мостов.
- В США повсеместно используется при возведении помещений для МРТ (магнитно-резонансной томографии).
- Применение при строительстве крупнейших мировых метрополитенов — в Берлине и Лондоне, Бангкоке, Нью-Дели и Гонконге.
Рассмотрим мировой опыт применения стеклопластиковой арматуры в строительстве на наглядных примерах.
Промышленные сооружения
Niederrhein Gold (Моерс, Германия), 2007 — 2009
Неметаллическое армирование для предупреждения трещинообразования. Армируемая площадь — 1150 м².
Фундамент для сталеплавильной печи диаметром 3,5 метра.
Здания исследовательских центров
Центр квантовых нанотехнологий (Ватерлоо, Канада), 2008.
Композитная арматура применяется для бесперейбойной работы приборов во время проведения научно-исследовательских работ.
Институт изучения твердых тел Макса Планка (Штутгарт, Германия), 2010-2011.
Композитная стеклопластиковая арматура используется в строительстве лаборатории высокой точности.
Автостоянки и вокзалы
Вокзал (Вена, Австрия), 2009.
Во избежание проникновения индукционных токов из прилегающего тоннеля метро, армирование буронабивных свай и стен нижних этажей выполнено без применения стали.
Крытый паркинг при торговом центре «Форум Штеглиц» (Берлин, Германия), 2006.
Применяется сетка из стеклопластиковой арматуры Ø 8 мм. Задачи армирования — коррозионная стойкость и предупреждение трещинообразования. Армируемая площадь — 6400 м².
Мостостроение
Мост Irvine Creek (Онтарио, Канада), 2007.
Используется арматура Ø 16 мм с целью предупреждения трещинообразования.
Мост 3rd Concession Bridge (Онтарио, Канада), 2008.
Арматура из стекловолокна используется при армировании переходных плит и соединений с мостовым покрытием.
Парапет на Walker Road (Канада), 2008.
Отбойник на мосту Essex County Road 43 (Виндзор, Онтарио), 2009.
Строительство моста (Небраска, США).
Укладка ж/д полотна и путей
Университетская площадь (Магдебург, Германия), 2005.
Окружная железная дорога (Гаага, Нидерланды), 2006.
Вокзальная площадь (Берн, Швейцария), 2007.
Трамвайная линия 26 (Вена, Австрия), 2009.
Опорная плита ж/д полотна (Базель, Швейцария), 2009.
Морские сооружения
Набережная (Блэкпул, Великобритания), 2007-2008.
Совместное использование с металлической арматурой.
Королевская вилла (Катар), 2009.
Подземное строительство
Коллектор WSK-E (Вена, Австрия), 2004.
Линия Север-Юг (Амстердам, Нидерланды), 2004-2006.
Участок тоннеля «Север» (горный перевал Бреннер в Альпах), 2006.
DESY Los 3 (Гамбург, Германия), 2009.
Эмшерканал (Боттроп, Германия), 2010.
Эксперты из США о композитной арматуре
Как видите, композитная стеклопластиковая арматура широко применяется в Европе и странах Америки. Неудивительно, ведь на Западе умеют считать деньги и знают, что такое эффективное строительство.
С опытом применения стеклопластиковой арматуры в России вы можете ознакомиться в разделе «Объекты», где мы показываем как используется наша продукция в строительстве.
Читайте также:
Защитный слой бетона
Армирование стяжки — назначение, технология, материалы
Как правильно выбрать стеклопластиковую арматуру
Применение композитной арматуры | ЯРКОМПОЗИТ
Технические характеристики позволяют применять ее в промышленно-гражданском строительстве и поверхностных слоях бетонной конструкции, для дорожного строительства, усиления мостов, в конструкциях, работающих в условиях ускоренной коррозии.
Стеклопластиковая арматура для бетона
На сегодняшний день арматура из стеклопластика (АСП) широко применяется в гражданском и промышленном строительстве. Это обусловлено целым рядом факторов:
- низкий удельный вес АСП;
- высокая коррозийная стойкость;
- низкая теплопроводность композитных материалов;
- высокая прочность АСП, в несколько раз превышающая прочность стальной арматуры;
- диэлектричность стеклопластиковой арматуры.
Как известно, главный недостаток традиционной арматуры из низкоуглеродистой стали – это низкий показатель устойчивости к коррозии, это ограничивает ее использование при строительстве морских сооружений и конструкций, находящихся в зоне переменного уровня воды. Применение поверхностного стеклопластикового армирования может решить проблему долговечности морских сооружений – в таком случае бетон не подвергается воздействию агрессивной среды.
Перспективы использования АСП для армирования бетонных конструкций рассмотрены во многих исследовательских работах отечественных НИИ (например, НИИЖБ, ХИСИ СибНИИЭ и т. д.), а также подтверждены многолетним опытом зарубежных стран.
Стеклопластиковое армирование
Армирование конструкций стеклопластиковой арматурой бывает трех основных видов: внутренним, внешним и комбинированным.
1. Внутреннее армирование АСП.
Основная область применения – для армирования конструкций, в которых среда агрессивна к арматуре, а не к бетону, что затрудняет использование стальной арматуры. Внутреннее неметаллическое армирование бывает:
- Дискретным – армирование осуществляется стеклопластиковыми стержнями, равнозначными стальным по прочности.
- Дисперсным – армирование производится путем добавления в бетонную смесь рубленных стеклопластиковых волокон (фибр). В таком случае волокна распределяются в бетоне хаотично, однако при использовании специальных мер можно добиться того, что фибры будут иметь определенное направление.
2. Внешнее армирование АСП.
Основная область применения – при строительстве сооружений, где среда является агрессивной к бетону. Внешнее армирование основано на использовании внешней листовой арматуры, создающей защитную воздухонепроницаемую и водонепроницаемую оболочку для бетона и выполняющую свою непосредственную армирующую функцию.
Внешнее армирование АСП бывает:
- Сплошным – выполняется при помощи сплошного листового материала;
- Дискретным – осуществляется с использованием отдельных полосок или сеток.
Бетонные конструкции в стеклопластиковых оболочках изготавливаются двумя основными способами. В первом случае оболочка из АСП наносится на предварительно высушенные бетонные элементы путем обматывания, а во втором – стеклопластиковая оболочка изготавливается заранее, а впоследствии заливается бетонной смесью.
3. Комбинированное армирование АСП.
При возведении конструкций, в которых для восприятия механических нагрузок недостаточно только внешнего армирования, дополнительно может применяться внутренняя стержневая арматура, причем она может быть как пластиковой, так и стальной.
Предварительное напряжение арматуры
Применение АСП целесообразно только в предварительно напряженных конструкциях, так как модуль деформации стеклопластиковых стержней в несколько раз меньше (в 4-5 раз), чем металлических. В случаях с арматурой из стеклопластика чаще всего применяются три основных способа предварительного напряжения бетонных конструкций:
Натяжение на упоры.
Данный способ предполагает вытягивание арматуры на нужную величину при помощи специальных приспособлений с последующим бетонированием и термовлажностной обработкой бетона для более быстрого отвердения.
Натяжение на бетон.
При натяжении стеклопластиковой арматуры на бетон в последнем проделываются специальные каналы для прокладки АСП. Натяжение арматуры осуществляется при помощи гидравлических домкратов. Для закрепления арматуры в каналы инъецируется петролатум.
Непрерывная навивка.
Данный способ, который, к слову сказать, не нашел широкого применения в современном строительстве, заключается в навивке на бетонное изделие гибких стержней или лент из стеклопластика.
Влияние температур на прочность арматуры
Показатель прочности АСП изменяется пропорционально изменению температуры:
- При понижении температуры до -40 градусов по Цельсию прочность стеклопластиковой арматуры увеличивает приблизительно на 40%
- При увеличении температуры свыше +20 градусов по Цельсию (вплоть до +300) прочность АСП постепенно уменьшается на 60%.
Изменение характеристик прочности АСП, происходящие вследствие колебания температур в пределах -40…+300 градусов Цельсия, являются обратимыми.
Стеклопластиковая арматура и ремонт ЖБК
Традиционно для восстановления ЖБ конструкций используются достаточно трудоемкие и затратные методы, зачастую требующие остановки производства. В сравнении с ними, внешнее стеклопластиковое армирование отличается не только повышенной коррозийной стойкостью и высокой прочностью, но и малыми сроками ремонтных работ. Именно эти показатели обуславливают рациональность применения ПАК для восстановления и усиления несущих элементов ЖБ сооружений.
В завершении стоит отметить, что использование стеклопластиковой арматуры, благодаря ее высокой коррозийной стойкости, не только существенно продляет срок эксплуатации бетонных конструкций, но и практически ликвидирует затраты на капитальные ремонты сооружений.
Композитные материалы | Типы композитов
Композитные материалы | Виды композитов | Приложения- Дом
- Композиты
- Композитные материалы | Виды композитов | Приложения
Композиты
3 сентября 2021 г.
Композитные материалы | Виды композитов | Применение
Введение в состав композитного материала sКомпозитный материал определяется как материал, образованный объединением двух или более различных материалов/компонентов, макроскопически отличающихся по своим свойствам и не растворяющихся друг в друге.
Комбинация различных компонентов в композитах придает композитному материалу уникальные свойства, отличные от отдельных компонентов.
Примером композитов являются глиняные строительные кирпичи, используемые с древних времен, которые образуются путем соединения сырцовых кирпичей и соломы. Это позволило композиту иметь прочность и сопротивление сырцовых кирпичей и прочность на растяжение соломы.
В общем, композиционный материал включает три основных компонента (а) матрицу, непрерывную фазу; (b) армирование, непрерывная или прерывистая фаза, используемая для усиления композита, и (c) область тонкого интерфейса.
На протяжении тысячелетий композитные материалы играли решающую роль в жизни человека, начиная с того, что позволили ранним цивилизациям строить дома, и заканчивая тем, что сделали возможными достижения в области современных технологий.
В повседневной жизни люди используют композитные материалы, в том числе керамическую плитку в ванной, которая помогает нам оставаться сухими.
Композиты действительно можно найти в большинстве обычных продуктов, включая строительные и инженерные проекты, медицинские приложения, энергетику и транспорт, спорт, авиацию, автомобилестроение и другие области.
Человечество использует композитные материалы тысячи лет. Первый композит был найден в 1500 году до нашей эры, когда египтяне и жители Месопотамии использовали глину и солому для строительства своих домов.
Монголы разработали первый лук, используя дерево, кость и животный клей. Во время Второй мировой войны цивилизация композитов была усовершенствована и перенесена из лаборатории в реальное производство. Также промышленностью была освоена разработка компонентов из армированных волокном полимерных композитов.
К 1945 году использование армированных волокном полимерных композитов стало использоваться в основном в военных целях.
В 1946 году был представлен первый композитный корпус лодки FPR, а к 1947 году кузов автомобиля был изготовлен из композитного материала и успешно прошел испытания.
Типы композитов Материал матрицы Основная функция материала матрицы в полимерном композите заключается в том, чтобы действовать как связующее и передавать нагрузку между компонентами композита, придавая компоненту его чистую форму и определяя качество его поверхности.
Полимерные композиты обычно используют два типа матричного материала, а именно. термопластичные и термореактивные. С самого начала композитной эры оба материала использовались для разработки композитов.
Характеристика термопластического и термосетирования заключается в следующем:
Thermoplastic | Thermosetting | ||
ВВЕДЕНИЯ | |||
ВВЕДЕНИЯ | |||
ВВЕДЕНИЯ | |||
ВВЕДЕНИЯ | |||
. держать нужную форму. Он имеет одно- или двумерную молекулярную структуру и имеет тенденцию к завышенной температуре плавления при повышенной температуре. | Термореактивные материалы выдерживают необратимую реакцию химической связи, т. е. сшивание или отверждение во время процесса для перехода фазы из жидкого состояния в твердое. Сшивание позволяет исключить переплав компонентов при подводе тепла.![]() | ||
Преимущества | Может быть переработан Возможность повторного формования и изменения формы с применением тепла Простота быстрого производства в больших объемах Химическая стойкость и ударопрочность Более высокая стоимость, чем у реактопластов Экологически безопасная обработка Прилипание к металлу | не может быть переработано после излечения, чем не может быть изменено или повторно затрат на стабильность. термопластический материал, используемый в полимерных композитах: Акрилонитрил-бутадиен-стирол (АБС) Полиметилметакрилат (ПММА) (акрил) Полибензимидазол Полиэтиленовый гомополимерный сополимер Полиуретан-стирол Акрилонитрил Полипропилен (ПП) Полиамид (ПА) Поликарбонат (ПК) Полиэфирэфиркетон (ПЭЭК) Полимолочная кислота Кислота (PLA) Поливинилхлорид (ПВХ) Тефлон | Some thermosetting material used in polymer composites: ResinUnsaturated polyesterVinyl esterPhenolSiliconeCyanate estersMethyl Methacrylate (MMA)Bismaleimide (BMI)Urea FormaldehydeFluoropolymersMelamine |
In fiber-reinforced polymer composites, different types of fibers can be используется как армированный материал. Выбор армированного материала зависит от конечного применения компонента/материала. Некоторое обычное волокнистое армирование выглядит следующим образом:
Как следует из названия, волокно получают из стекла на основе диоксида кремния или другого состава путем нагревания до 1675°C. Доступны различные типы стекловолокна в зависимости от их свойств.
- А-стекло (щелочное стекло): хорошая химическая стойкость, но более низкие электрические свойства.
- C-стекло (химическое стекло): высокая химическая стойкость
- E-стекло (электростекло): отличный изолятор и водостойкость.
- S-Glass (структурное стекло): хорошие механические свойства.
- D-стекло (диэлектрическое стекло): хорошие электрические свойства, но плохие механические свойства по сравнению со стекловолокном E & S
- Стекловолокно E-CR (электронное стекловолокно): электрическое сопротивление, химическая стойкость, хорошие механические свойства , водонепроницаемость по сравнению с E-стеклом
- AR-стекло (щелочестойкое стекло): специально для бетона.
Придает бетону прочность и гибкость, предотвращая растрескивание
- M-стекловолокно: в его состав входит бериллий, который обеспечивает лучшую эластичность по сравнению с E-стеклом
- Z-стекловолокно : используется для производства прозрачных компонентов, устойчивых к механическим воздействиям, воздействию УФ-излучения, кислоты, щелочи, соли, царапин , износостойкость и термостойкость, используемые в нити для 3D-принтеров
Углеродное волокно состоит из атомов углерода, связанных вместе, образуя длинную цепь. Углеродные волокна чрезвычайно жесткие, прочные и легкие по сравнению со стекловолокном.
Волокна чрезвычайно жесткие, прочные, с низким отношением веса к прочности, низким коэффициентом теплового расширения и обладают хорошей устойчивостью к химическим веществам и высоким температурам.
Углеродное волокно было впервые изобретено недалеко от Кливленда, штат Огайо, в 1958 году.
На основании модуля, прочности и конечной температуры термообработки углеродные волокна можно разделить на следующие категории:
Арамидные волокнаКевлар производится из ароматических полиамидных (арамидных) волокон, которые DuPont сделала общедоступными в начале 1970-е годы.
Кевларовое волокно обладает высокой прочностью, хорошей стойкостью к истиранию, химической стойкостью, непроводимостью, низкой воспламеняемостью и хорошей целостностью ткани при повышенных температурах. Арамидное волокно обычно доступно в желтом цвете и широко используется в тех случаях, когда требуется высокая прочность и малый вес.
Благодаря хорошей ударопрочности свойство кевларового волокна используется в баллистических целях
В зависимости от расположения химической связи в структуре кевларовое волокно подразделяется на два типа:
- Мета-арамид : Химическая связь мета-арамида имеет зигзагообразную форму, а прочность на растяжение мета-арамидного волокна ниже, чем у пара-арамида.
Эти волокна обладают хорошей термической, химической и радиационной стойкостью.
- Параарамид : В параарамидном волокне структуры химических связей выровнены в продольном направлении волокна. Этот тип волокна обладает высокой прочностью на растяжение. Такое волокно широко используется в строительных конструкциях
Композиты, армированные натуральным волокном, в последние годы стали чрезвычайно популярными для многих применений благодаря своим хорошим характеристикам.
В связи с государственной политикой и заботой об окружающей среде увеличивается использование натурального волокна в полимерных композитах.
Натуральные волокна имеют низкую плотность, высокую удельную прочность и обеспечивают хорошую тепло- и звукоизоляцию. Натуральное волокно получают либо из растений, либо из животных.
Эти волокна имеют преимущество перед синтетическими волокнами в различных секторах, таких как автомобильная, строительная и спортивная промышленность, благодаря своим механическим свойствам, сравнимым со стеклянным волокном.
.0063
- Space: antenna, radar, satellite structures , солнечные отражатели и т. д.
- Самолеты: аэродинамические поверхности, лопасти компрессоров, дверцы моторных отсеков, лопасти вентиляторов, валы винтов вертолетов, лопасти турбин, валы турбин, конструкции кессона крыла и т. д.
- Автомобили: кузов автомобиля, бампер, брызговики, дверные панели, приборная панель, карданный вал, топливный бак, баллон СПГ, шасси, крыло и т.д. .
- Спорт: лыжи, доски для серфинга, виндсерфинг, доски для настольного тенниса, рейки и лонжероны для планирующих крыльев, теннис, бадминтон, удочки, клюшки для гольфа, бейсбольные биты, хоккейные клюшки, древко, меч и т.
д.
Компания ATIRA была объявлена Министерством текстиля правительства Индии «Центром передового опыта в области композитов» в марте 2011 года. для достижения снижения веса, высоких механических свойств, конкурентоспособности по стоимости и расширения базы знаний в области композитов посредством исследований, разработок и обучения.
Работа, выполненная в ATIRA (Композитные материалы)- Продукты на основе углеродного волокна и эпоксидной смолы, полученные методом вакуумной инфузии. Разработаны различные компоненты для систем спутниковой связи. Эти работы были выполнены для SAC-ISRO Ahmedabad.
- Системы спутниковой связи также были разработаны с использованием углеродно-эпоксидных препрегов.
- Углеродный материал сердцевины находится в стадии разработки для изготовления однородных сэндвич-панелей с улучшенными эксплуатационными характеристиками.
- Натуральные волокна, такие как джут и композиты на основе хлопка, были разработаны с использованием процесса компрессионного формования. Они находят применение в перегородке, двери и машиностроении.
- Композитные профили на основе пултрузии, разработанные для разнообразных применений, таких как строительство зданий, мебель, градирни и т. д.
- Композиты, формованные под давлением, на основе синтетического армирования, такого как стекловолокно, углеродное волокно, арамид и т. д., и натурального армирования, такого как хлопковое волокно , джутовое волокно и т. д. были разработаны для разнообразных применений.
- Процесс, основанный на вакуумной инфузии (VARI), используемый для разработки космических и авиационных изделий на основе углеродных, арамидных и эпоксидных систем. Также была разработана сэндвич-структура на основе алюминиевых сот, углеродного и кварцевого сердечника и т. д.
Если вы заинтересованы в получении дополнительной информации, пожалуйста, напишите на композиты research@atira. in
СПИСОКТ:
NGO. Знакомство с композиционными материалами. Композитные и нанокомпозитные материалы: от знаний к промышленному применению. 2020 25 февраля.
Добавить Автора
Готово на 70%
Почти готово!
Заполните форму ниже, чтобы загрузить прямо сейчас.
🔒Ваши данные в безопасности.

Готово на 70%
Почти готово!
Заполните форму ниже, чтобы загрузить прямо сейчас.
🔒Ваши данные в безопасности.
Готово на 70%
Почти готово!
🔒Ваши данные в безопасности.
Готово на 70%
Почти готово!
Заполните форму ниже, чтобы загрузить прямо сейчас.
🔒Ваши данные в безопасности.
Готово на 70%
Почти готово!
Заполните форму ниже, чтобы узнать сейчас.
🔒Ваши данные в безопасности.
Готово на 70%
Почти готово!
Заполните форму ниже, чтобы узнать сейчас.
🔒Ваши данные в безопасности.
Готово на 70%
Почти готово!
Заполните форму ниже, чтобы узнать сейчас.
Готово на 70%
Почти готово!
Заполните форму ниже, чтобы узнать сейчас.
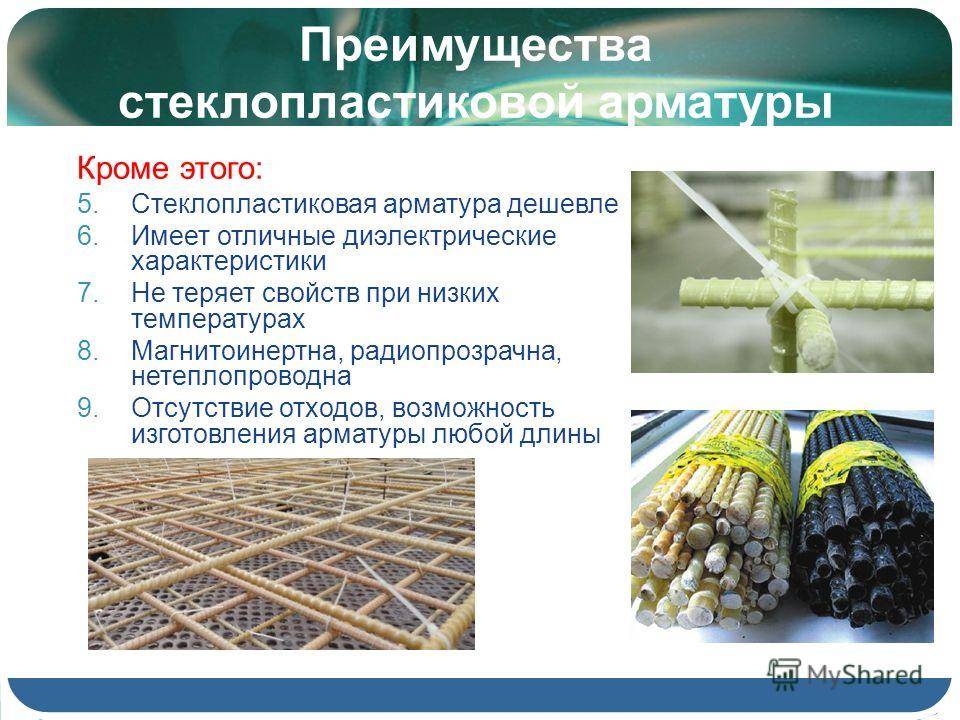
Готово на 70%
Почти готово!
Заполните форму ниже, чтобы узнать сейчас.
Требования к обслуживанию
—Испытания волоконИспытания пряжиИспытания тканей и одеждыФункциональный текстильИспытания защитного текстиляГеосинтетикаНетканые материалы
🔒Ваши данные в безопасности.
Композиты
Композит изготавливается путем физического объединения двух или более материалов (компонентов) для получения комбинации (смеси) структурных свойств, отсутствующих у какого-либо отдельного компонента. Например, они могут обеспечить большую прочность и жесткость, чем любой из отдельных компонентов, при этом будучи максимально легкими.
Композиты все чаще разрабатываются для решения множества задач. Например, композиты, армированные волокном, используются для замены таких материалов, как металлы и их сплавы.
Композиты предназначены для обеспечения:
- малого веса
- жесткость и прочность
- низкий коэффициент расширения
- сопротивление усталости
- простота изготовления сложных форм
- простой ремонт поврежденных конструкций
- устойчивость к коррозии
Существует множество различных типов композитов. В этом разделе рассматриваются два наиболее важных элемента, которые в настоящее время разрабатываются для различных целей:
- Полимерные композиты, армированные волокном
- Композиты, армированные частицами
Фазы в композитах
Композиты, армированные волокнами и частицами, обычно состоят из более или менее непрерывной фазы. Это непрерывная фаза также известен как матрица , а материал, распределенный по матрице, известен как дисперсная фаза (рис. 1).
Рисунок 1, иллюстрирующий фазы композита.
Дисперсную фазу иногда называют армирование , если это фаза, добавляемая для повышения прочности. В качестве альтернативы его называют наполнителем , если он добавляется для других целей, например, для увеличения объема матрицы при низких затратах, не влияющих на свойства композита. Также может быть фаза для создания связи между слоями или фазами, иногда называемая 9-й.0117 интерфейс .
При разработке композитов необходимо учитывать следующие факторы:
- Соотношение матрицы и дисперсной фазы может варьироваться в зависимости от предполагаемого использования композита. Матричная фаза может представлять собой сыпучий материал с диспергированными в нем частицами или волокнами. Это также может быть второстепенная фаза, больше похожая на клей, скрепляющий частицы или волокна вместе, обеспечивающий жесткость в противном случае очень гибким массивам волокон и придающий структуру тому, что в противном случае было бы рыхлыми частицами.
Матрица также служит для защиты дисперсной фазы от механических повреждений и химического воздействия. Если матрица пластична, она предотвращает распространение трещин между волокнами или частицами, даже когда она подвергается сильному износу.
- Размер и форма частиц и волокон дисперсной фазы определяют, насколько плотно они могут быть упакованы. Хотя более мелкие частицы обеспечивают большую площадь поверхности для контакта с матрицей, более длинные волокна обеспечивают лучшее армирование. Необходимо соблюдать баланс.
- Поверхность раздела между матрицей и дисперсной фазой также влияет на общие характеристики композита. Прочность композита зависит не только от свойств матрицы, но и от того, насколько хорошо она сцепляется с частицами и волокнами дисперсной фазы.
Полимерные композиты, армированные волокном
Полимерные композиты, армированные волокном (FRP, также известные как композиты с полимерной матрицей (PMC)) подразделяются на:
a) Полимерные композиты, армированные углеродным волокном (CFRPs)
b) Полимерные композиты, армированные стекловолокном ( GFRPs)
c) Полимерные композиты, армированные арамидными волокнами (AFRPs)
В каждом случае волокно заключено в полимерную матрицу (непрерывная фаза). Эти матрицы обычно представляют собой акрилэпоксифенольные или полиэфирные смолы.
Производство
Производство композита, армированного волокном, включает несколько стадий, в ходе которых производится производство наполнителя (волокна), а затем, при необходимости, его выравнивание перед введением матрицы.
Волокна из полимеров (например, из арамидов, см. ниже), стекла и металлов могут быть получены из расплавленного состояния путем их вытягивания. Большинство углеродных волокон сначала вытягивают из полимера, например поли(пропенонитрила) (полиакрилонитрила), который затем окисляют с последующим пиролизом. Если волокна не выровнены (произвольная ориентация) друг с другом, наполнитель и матрица могут быть смешаны вместе в виде порошков или суспензий, сформованы или отлиты в форму, а матрица затвердевает и связывается с наполнителем за счет нагревания или химической реакции. Формование может быть осуществлено литьем под давлением или литьем композита. При необходимости перед любой дальнейшей обработкой выполняется дополнительная механическая обработка для упрочнения композита.
Производство композитов с ориентированным волокном (рис. 1) является более сложным. Волокна могут быть использованы в виде мононити или могут быть скручены в пряжу до 10 000 нитей. Затем нити ткут или вяжут в двух- или трехмерные ткани, а затем могут формировать ленты путем плетения или плетения. Нити также можно перерабатывать в нетканые маты из волокон, произвольно ориентированных в двух измерениях.
Маты, ленты и ткани могут быть пропитаны материалом матрицы (или материалами, из которых изготовлена матрица) перед окончательной сборкой и обработкой, и тогда они обозначаются как препрег ( препрег -им препрег нат ).
Таким образом, нет необходимости обращаться с отдельными химическими веществами. Его просто раскатывают и используют как ламинат. Отверждение осуществляется путем нагревания.
Ткани и циновки укладываются в формы, иногда вручную, пропитываются матричным материалом и обрабатываются. Они могут быть спрессованы механически или методами формования под давлением или вакуумом. Нити или ленты также можно наматывать, пропуская через ванну с матрицей перед обработкой в твердую форму.
Простым примером препрега является повязка, которая используется для фиксации сломанных конечностей (Единица 67). Повязка изготовлена из полиэстера и пропитана линейным полиуретаном, матрицей. Повязка, препрег, гибкая и наматывается на сломанную конечность. При замачивании молекулы полиуретана реагируют с водой, образуя поперечные связи между молекулами, создавая прочный, но легкий отлив.
(a) Полимерные композиты, армированные углеродным волокном (CFRPs)
Углеродные волокна, как правило, изготавливаются путем нагрева нитей поли(пропенонитрила) (полиакрилонитрила, ПАН) при температуре ca 500 K в атмосфере воздуха с образованием окисленного ПАН. Окисленный ПАН затем помещают в печь с инертной атмосферой газа, такого как аргон, и нагревают до 90 117 или 90 118 2000 К, процесс, известный как пиролиз, нагревание вещества в отсутствие воздуха. Продукт, углеродное волокно, содержит цепочки атомов углерода, которые связаны друг с другом (лестничные полимеры), образуя узкие листы атомов углерода толщиной в один атом, известные как графен. Выделение графена профессорами Андреем Геймом и Константином Новоселовым из Манчестерского университета настолько важно, что в 2010 году эти два ученых были удостоены Нобелевской премии по физике9.0011
Можно представить его как кусок куриной сетки в очень маленьком (атомарном) масштабе. Графен также является базовой структурой графита и углеродных нанотрубок. В случае с углеродным волокном листы сливаются, образуя единую круглую нить. Углеродные волокна используются в качестве наполнителя в сплошной матрице полимера, часто эпоксидной смолы. Слои ткани из углеродного волокна укладываются в требуемой форме, обычно в форме, которая затем заполняется эпоксидной смолой и нагревается.
Использование
Композиты из углеродного волокна являются относительно дорогими строительными материалами и поэтому используются, когда их свойства легкости и прочности имеют первостепенное значение. Примеры использования включают высококачественное спортивное оборудование, такое как рамы теннисных ракеток, клюшки для гольфа и удочки, а также ноутбуки и фотоаппараты.
Они также широко используются в конструкции самолетов. Фюзеляжи новейших коммерческих самолетов (Boeing 787 (Dreamliner) и Airbus A350) изготавливаются в основном из углепластика из-за его превосходной легкости и прочности.
Другое свойство углепластиков используется в тормозах самолетов. Они необходимы для быстрого поглощения значительного количества энергии без механического отказа или заедания. Обычная конструкция основана на нескольких вращающихся и стационарных дисках, температура поверхности которых может достигать 3000 К. Поэтому материал диска должен обладать отличной термической и ударной стойкостью, жаропрочностью и хорошей теплопроводностью. Углерод является идеальным материалом, а диски изготовлены из углеродного композита, в котором наполнитель — углеродное волокно, а матрица — углерод, полученный в результате пиролиза метана. Кроме того, они весят примерно на 30 % меньше, чем стальные диски, что значительно экономит топливо.
В течение многих лет углепластики также использовались для изготовления кузовов гоночных автомобилей Формулы-1, обеспечивая водителям более надежную защиту даже при авариях на скорости более 300 км/ч -1 . В настоящее время они используются в роскошных автомобилях (часть модельного ряда Mercedes Benz и для крыши GM Corvette ZR1) и в качестве защитного снаряжения для мотоциклистов.
Углепластики все чаще используются для «модернизации» существующих крупных конструкций, таких как мосты из железобетона. Ткань из углеродного волокна обернута вокруг частей, которые нуждаются в укреплении.
(b) Полимерные композиты, армированные стекловолокном (GFRP)
Стекловолокно изготавливается из кремнезема (песка), карбоната натрия и карбоната кальция вместе с другими соединениями для придания требуемых конкретных свойств. Материалы нагревают примерно до 1700 К в печи, а затем выдавливают прямо из печи через металлические отверстия (сплав платины/родия) различного диаметра (4-34 мкм) для получения нитей. Высокоскоростная намоточная машина, вращающаяся быстрее, чем выходящее расплавленное стекло, натягивает их в очень тонкие нити. Количество отверстий варьируется от 200 до 8000.
Нити покрыты смазкой для их защиты и собраны вместе на барабане, похожем на катушку нити.
В стеклопластике, в котором стекловолокно является наполнителем (дисперсной фазой), матрица обычно представляет собой полиэфирную смолу, хотя также используются эпоксидные и акриловые полимеры.
Применение
Стеклопластики широко используются в производстве лодок по соображениям стоимости и технического обслуживания. В то время как большие корабли обычно строятся из стали, более 80% морских корпусов длиной менее 40 м изготовлены из полимера, армированного стекловолокном. Это гораздо более дешевый процесс, а корпус легче обслуживать. Кроме того, существуют определенные приложения, в которых магнитные, электрические или тепловые свойства стеклопластика являются предпочтительными, например, тральщики, которые должны быть немагнитными, чтобы избежать активации мин.
Препреги стеклофенольной смолы также используются для улучшения защиты бронированных транспортных средств.
(c) Полимерные композиты, армированные арамидом (ARPC)
Арамид представляет собой полимерный ароматический амид. Кевлар ® является особенно широко используемым арамидом.
С ним очень трудно обращаться, так как единственным эффективным растворителем является концентрированная серная кислота. Кевлар ® сделан из легких атомов, но очень прочен и гибок, по весу в пять раз прочнее стали. Его прочность обусловлена тем, как выровнены полимерные цепи, а плоские молекулы удерживаются вместе водородными связями. Эти слои молекул могут складываться вдоль оси волокна (рис. 2).
Эти уже прочные волокна используются в качестве наполнителя в ARPC с фенольной смолой или эпоксидной смолой в качестве матрицы. Они особенно полезны там, где необходимо поглощать и рассеивать энергию, а также способны противостоять истиранию.
Рис. 2 Структура кевлара ® .
Применение
Эти композиты широко используются в авиации, для лопастей винтов вертолетов, в спорте, для изготовления ракеток для тенниса, бадминтона и сквоша, а также в лодках, таких как каяки и лодки.
Рисунок 3 Кевлар ® и другие полиароматические амиды также используются в качестве волокон в тканях для защитной одежды. Их огнестойкие свойства позволяют использовать их пожарными, а их прочность означает, что они используются для бронежилетов.
|
Композиты, армированные частицами (PRC)
По существу существует два типа композитов, армированных частицами: композиты, армированные крупными частицами, и композиты, армированные мелкими частицами. Материалы классифицируются не строго по физическим размерам частиц, а по механизму армирования. В материале, армированном небольшими частицами, механизм находится на молекулярном уровне, и частицы могут диспергироваться в матрице или осаждаться из нее.
Армирование крупными частицами, как следует из названия, включает более крупные частицы и распределение нагрузки между фазами. Какой бы ни была их геометрия, частицы малы по сравнению с размером структуры и равномерно распределены по ней.
Частицы могут повысить прочность композита на излом по сравнению с матрицей, предотвращая или препятствуя распространению трещин через матрицу, либо физически блокируя и останавливая трещины, либо отводя и расщепляя их, чтобы препятствовать их продвижению по изделию. Они также могут улучшить жесткость и прочность композита по сравнению с матрицей, выдерживая часть нагрузки.
Использование
Бетон — это простой, повседневный пример PRC, состав которого варьируется в зависимости от его предполагаемого использования. Наиболее распространенной матрицей является портландцементная паста, которая подвергается химическим реакциям, приводящим к схватыванию в течение нескольких часов, а твердение продолжается в течение нескольких недель или месяцев. Этот материал армирован заполнителем (дисперсной фазой), таким как галька или щебень (1-2 см) и песок (1-2 мм). Помимо усиления, дисперсная фаза дает и другие преимущества. Реакции начального схватывания бетона экзотермические, и при использовании только цемента и воды это приводит к проблемам с отводом тепла и растрескиванию. Добавление заполнителя решает эту проблему, действуя как поглотитель тепла, уменьшая скорость и величину повышения температуры.
Бетон часто содержит дополнительную фазу в виде стальной проволоки, стержней или троса для придания еще большей прочности.
Тугоплавкие карбиды представляют собой твердые износостойкие керамические материалы, такие как карбиды титана и вольфрама (TiC и WC). Они могут быть включены в матрицу металла, часто кобальта или никеля, для изготовления режущих наконечников станков. Это пример металлокерамики, комбинации керамики и металла. Карбид обеспечивает износостойкую режущую кромку, но сам по себе может разрушиться при ударе по металлу, которому придается форма. Металлическая матрица повышает устойчивость и проще в изготовлении. Со временем, когда частицы смещаются, новые обнажаются, чтобы сохранить острую режущую кромку, что делает инструмент в некоторой степени самозатачивающимся.
Технический углерод по существу состоит из сферических частиц углерода, образующихся при сжигании нефти или газа с ограниченным поступлением кислорода, и часто известен как печная сажа. Наиболее важным применением частиц является армирующая фаза в виде частиц в каучуке, используемом при производстве шин. Шины могут быть изготовлены из различных смесей натурального каучука и синтетических каучуков, смесь зависит от ее предполагаемого использования (например, для боковины, протектора или внутренней обшивки).
Синтетические каучуки включают:
- поли(бута-1,3-диен)
- поли(2-метилбута-1,3-диен) (полиизопрен)
- сополимеры фенилэтена (стирола) и бут-1,3-диена
- бромированные сополимеры 2-метилпропена (изобиутен) и изопрена
Использование технического углерода в резине повышает износостойкость.