Применение композитной арматуры в строительстве
Композитная (стеклопластиковая) арматура
Пластик да нитки
Изобретение композитной арматуры
Знатоки строительного дела относят к 60-м годам прошлого столетия. В этот период в США и в Советском Союзе были начаты активные исследования ее свойств.
Однако, несмотря на достаточно солидный возраст, данный материал до сих пор не знаком большинству застройщиков. Восполнить пробел знаний о стеклопластиковой арматуре, ее свойствах, во всех достоинствах и недостатках вам поможет разобраться МодульСтрой.
Попутно отметим, что материал этот весьма спорный. Производители хвалят его на все лады, а строители-практики относятся с недоверием. Простые граждане смотрят на тех и на других, не зная кому верить.
Что такое композитная арматура, как она производится и где применяется?
Коротко структуру композитной арматуры можно охарактеризовать как «волокно в пластике». Ее основа – стойкие к разрыву нити из углерода, стекла или базальта. Жесткость композитному стержню придает эпоксидная смола, обволакивающая волокна.
Для лучшего сцепления с бетоном на прутья наматывается тонкий шнур. Он сделан из того же самого материала, что и основной стержень. Шнур создает винтовой рельеф, как у стальной. Твердение эпоксидной смолы происходит в сушильной камере. На выходе из нее композитную арматуру немного вытягивают и нарезают. Некоторые производители до момента твердения полимера обсыпают пластиковые стержни песком для улучшения сцепления с бетоном гладких участков.
Область применения стеклопластиковой арматуры нельзя назвать очень широкой. Ее используют в качестве гибких связей между облицовкой фасада и несущей стеной, а также укладывают в дорожные плиты и опалубку резервуаров. В каркасах, усиливающих ленточные фундаменты и бетонные полы, пластиковую арматуру применяют не так часто.
Ставить композитные стержни в плиты перекрытия, перемычки и другие конструкции, работающие на растяжение, не рекомендуется.
Физические свойства композитной арматуры
Модуль упругости у полимерного композита существенно ниже, чем у стали (от 60 до 130 против 200 ГПа). Это значит, что там, где металл вступает в работу, предохраняя бетон от образования трещин, пластик еще продолжает сгибаться. Прочность на разрыв у стеклопластикового стержня в 2,5 раза выше, чем у стального.
Наименее прочная, но самая дешевая — арматура из стекловолокна и базальтовый композит. Самый надежный и вместе с тем самый дорогой материал делают на основе углеродного волокна.
К прочностным свойствам материала мы еще вернемся, когда будем сравнивать его с металлом.
А пока рассмотрим другие характеристики данного материала:
- К положительным качествам композита относится его химическая инертность. Он не боится коррозии и воздействия агрессивных веществ (щелочной среды бетона, морской воды, дорожных химреагентов и кислот).
- Вес пластиковой арматуры в 3-4 раза меньше, чем стальной.
- Низкая теплопроводность материала улучшает энергосберегающие характеристики конструкции (нет мостиков холода).
- Композитная арматура не проводит электричества. В конструкциях, где она используется, не возникает коротких замыканий электропроводки и блуждающих токов.
- Композитный пластик магнитноинертен и радиопрозрачен. Это позволяет использовать его в строительстве сооружений, где должен быть исключен фактор экранирования электромагнитных волн.
Стеклопластиковый стержень под 90 градусов на стройке не согнешь.
Недостатки композитной арматуры:
- Невозможность гибки с малым радиусом в условиях стройки. Гнутый стержень нужно заранее заказывать.
- Невозможность сваривать каркас (минус относительный, поскольку даже для стальной арматуры лучший способ соединения – вязка, а не сварка).
- Низкая термостойкость.
При сильном нагреве и пожаре бетонная конструкция, армированная композитными стержнями, разрушается. Стекловолокно не боится высокой температуры, но связующий ее пластик теряет прочность при нагреве выше +200 С.
- Старение. Общий минус всех полимеров. Неметаллическая арматура не исключение. Ее производители завышают срок эксплуатации до 80-100 лет.
Вязка пластиковыми хомутами или стальной проволокой – единственный возможный метод сборки каркаса.
Какая арматура лучше металлическая или стеклопластиковая?
Наше маленькое исследование наглядно иллюстрирует таблица реальной, а не теоретической равнопрочной замены стальной арматуры на композитную. Ей можно пользоваться при выборе и покупке.
Просмотрев данную таблицу, нетрудно заметить, что пластика для равноценной замены металла требуется не меньше, а больше металла. Только самый дорогой углеродоволоконный материал (АУК) превосходит сталь равного с ним диаметра.
Ассортимент и цена композитной арматуры
Самая востребованная на стройке – арматура из стеклопластикового композита. Ее сортамент и средние цены вы можете посмотреть в нашем прайс-листе на официальном сайте компании,или связаться с нашими операторами по телефону +7 (4852) 90-78-78, если у вас возникли вопросы.
Стеклопластиковая арматура: характеристики, применение, фото, видео
- Что собой представляет арматура из стеклопластика
- Особенности структуры
- Основные свойства
- Как и из чего производят стеклопластиковую арматуру
- Параметры – вес, диаметр, шаг навивки
- Виды стеклопластиковой арматуры и сферы ее применения
- Что лучше – стеклопластик или сталь?
Стеклопластиковая арматура, появившаяся на отечественном рынке относительно недавно, стала достойной альтернативой традиционным пруткам, изготовленным из металла. Стеклоарматура, как еще называют данный материал, обладает многими уникальными характеристиками, которые выгодно выделяют ее среди других изделий подобного назначения. Между тем подходить к выбору арматуры из стеклопластика следует очень взвешенно.
Стеклопластиковая арматура в пачках
Что собой представляет арматура из стеклопластика
Стеклопластиковая арматура, если разбираться в ее конструктивных особенностях, представляет собой неметаллический стержень, на поверхность которого нанесена навивка из стекловолокна. Диаметр спиралевидного профиля арматуры, изготовленной из композитных материалов, может варьироваться в интервале 4–18 мм. Если диаметр прутка такой арматуры не превышает 10 мм, то она отпускается заказчику в бухтах, если превышает – то прутками, длина которых может доходить до 12 метров.
Для изготовления композитной арматуры могут быть использованы различные типы армирующих наполнителей, в зависимости от этого она подразделяется на несколько категорий:
- АСК – изделия, изготовленные на основе стеклопластика;
- АУК – углекомпозитные армирующие изделия;
- АКК – арматура, выполненная из комбинированных композитных материалов.
На отечественном рынке наибольшее распространение получила стеклопластиковая арматура.
Различные стержни стеклопластиковой арматуры
Особенности структуры
Стеклопластиковая арматура – это не просто пруток из композитного материала. Она состоит из двух основных частей.
- Внутренний стержень представляет собой параллельно расположенные волокна стеклопластика, соединенные между собой при помощи полимерной смолы. Отдельные производители выпускают арматуру, волокна внутреннего ствола которой не параллельны друг другу, а завиты в косичку. Следует отметить, что именно внутренний стержень арматуры из стеклопластика формирует ее прочностные характеристики.
- Внешний слой арматурного прутка, изготовленного из стеклопластика, может быть выполнен в виде двунаправленной навивки из волокон композитного материала либо в виде напыления мелкофракционного абразивного порошка.
Стеклопластиковые арматурные стержни с абразивным напылением
Конструктивное исполнение арматурных прутков из стеклопластика, которое во многом определяет их технические и прочностные характеристики, зависит от фантазии производителей и применяемых ими технологий изготовления данного материала.
Основные свойства
Стеклопластиковая арматура, согласно результатам многочисленных исследований, проведенных компетентными организациями, обладает рядом характеристик, выгодно отличающих ее от других материалов подобного назначения.
- Арматурные прутки из стеклопластика обладают небольшой массой, которая меньше веса аналогичных изделий из металла в 9 раз.
- Стеклопластиковая арматура, в отличие от изделий из металла, очень устойчива к коррозии, отлично противостоит воздействию кислой, щелочной и соленой сред. Если сравнивать коррозионную устойчивость такой арматуры с аналогичными свойствами изделий из стали, то она выше в 10 раз.
- Свойство проводить тепло у стеклопластиковой арматуры значительно ниже, чем у изделий из металла, что минимизирует риск возникновения мостиков холода при ее использовании.
- За счет того, что арматура из стеклопластика транспортируется значительно проще, а срок ее эксплуатации значительно дольше, чем у металлической, ее применение более выгодно в финансовом плане.
- Стеклопластиковая арматура – это диэлектрический материал, который не проводит электрический ток, обладает абсолютной прозрачностью для электромагнитных волн.
- Использовать такой материал для создания армирующих конструкций значительно проще, чем металлические прутки, для этого нет необходимости в применении сварочного оборудования и технических устройств для резки металла.
Сравнительные характеристики стальной и стеклопластиковой арматуры
Благодаря своим бесспорным достоинствам стеклопластиковая арматура, появившись относительно недавно на отечественном рынке, уже успела завоевать высокую популярность как у крупных строительных организаций, так и у частных застройщиков. Между тем обладает такая арматура и рядом недостатков, к наиболее значимым из которых следует отнести:
- достаточно низкий модуль упругости;
- не слишком высокую термическую устойчивость.
Низкий модуль упругости стеклопластиковой арматуры является плюсом при изготовлении каркасов для укрепления фундамента, но большим минусом в том случае, если она используется для армирования плит перекрытия. При необходимости обращения в таких случаях именно к этой арматуре предварительно необходимо провести тщательные расчеты.
График замены стальной арматуры на композитную
Невысокая термическая устойчивость стеклопластиковой арматуры является более серьезным недостатком, ограничивающим ее применение. Несмотря на то, что такая арматура относится к категории самозатухающих материалов и не способна служить источником распространения огня при ее применении в бетонных конструкциях, при высоких температурах она утрачивает свои прочностные характеристики. По этой причине использоваться такая арматура может только для укрепления тех конструкций, которые не подвергаются воздействию высоких температур в процессе эксплуатации.
Еще одним значимым недостатком арматуры, изготовленной из стеклопластика, следует отнести то, что со временем она утрачивает свои прочностные характеристики. Этот процесс значительно ускоряется, если она подвергается воздействию щелочных сред. Между тем такого недостатка можно избежать, если применять стеклопластиковую арматуру, изготовленную с добавлением редкоземельных металлов.
Как и из чего производят стеклопластиковую арматуру
Многим стеклопластиковая арматура знакома не только по фото в интернете, но и на практике применения в строительстве, однако мало кто знает, как она производится. Технологический процесс производства арматурных прутков из стеклопластика, за которым очень интересно наблюдать по видео, легко поддается автоматизации и может быть реализован на базе как крупных, так и небольших производственных предприятий.
Технологическая линия производства стеклопластиковой арматуры
Для изготовления такого строительного материала прежде всего необходимо подготовить сырье, в качестве которого используется алюмоборсиликатное стекло. Чтобы придать исходному сырью требуемую степень тягучести, его расплавляют в специальных печах и уже из полученной массы вытягивают нити, толщина которых составляет 10–20 микрон. Толщина полученных нитей настолько невелика, что, если снять их на фото или видео, то без увеличения полученной картинки их не разглядеть. На стеклонити при помощи специального устройства наносится маслосодержащий состав. Затем из них формируются пучки, которые получили название стеклоровинга. Именно такие пучки, собранные из множества тонких нитей, являются основой стеклопластиковой арматуры и во многом формируют ее технические и прочностные характеристики.
Устройство подогрева и разделения нитей
После того как нити из стеклопластика подготовлены, они подаются на производственную линию, где их и превращают в арматурные прутки различного диаметра и разной длины. Дальнейший технологический процесс, познакомиться с которым можно по многочисленным видео в интернете, выглядит следующим образом.
- Через специальное оборудование (шпулярник) нити подаются на натяжное устройство, которое одновременно выполняет две задачи: выравнивает напряжение, имеющееся в стеклонитях, располагает их в определенной последовательности и формирует будущий арматурный стержень.
- Пучки нитей, на поверхность которых предварительно был нанесен маслосодержащий состав, обдаются горячим воздухом, что необходимо не только для их просушки, но и для незначительного нагревания.
- Прогретые до требуемой температуры пучки нитей опускаются в специальные ванны, где пропитываются связующим веществом, также нагретым до определенной температуры.
- Потом пучки нитей пропускаются через механизм, при помощи которого выполняется окончательное формирование арматурного стержня требуемого диаметра.
- Если изготавливается арматура не с гладким, а с рельефным профилем, то сразу после выхода из калибровочного механизма осуществляется навивка пучков из стеклонитей на основной стержень.
- Чтобы ускорить процесс полимеризации связующих смол, готовый арматурный пруток подается в туннельную печь, перед входом в которую на прутки, изготавливаемые без навивки, наносится слой мелкофракционного песка.
- После выхода из печи, когда стеклопластиковая арматура практически готова, стержни охлаждают при помощи проточной воды и подают на резку либо на механизм их сматывания в бухты.
Отрезной механизм – последнее звено в производстве композитной арматуры
Таким образом, технологический процесс изготовления стеклопластиковой арматуры не такой сложный, о чем можно судить даже по фото или видео его отдельных этапов. Между тем такой процесс требует использования специального оборудования и строгого соблюдения всех режимов.
На видео ниже можно более наглядно ознакомиться с процессом производства композитной стеклоарматуры на примере работы производственной линии ТЛКА-2.youtube.com/embed/tQ0cAKHciZ4″/>
Параметры – вес, диаметр, шаг навивки
Арматура, для изготовления которой используется стекловолокно, характеризуется рядом параметров, определяющих область ее применения. К наиболее значимым относятся:
- вес одного погонного метра арматурного прутка;
- для изделий с рельефным профилем – шаг навивки пучков стекловолокна на их поверхности;
- диаметр арматурного стержня.
На сегодняшний день арматура с рельефным профилем выпускается преимущественно с шагом навивки, равным 15 мм.
Выбор диаметра стеклопластиковой арматуры
Наружный диаметр арматурного прутка характеризуется номером, который присваивается изделию в соответствии с Техническими условиями производства подобной продукции. В соответствии с ТУ, арматурные прутки из стекловолокна сегодня выпускаются под следующими номерами: 4; 5; 5,5; 6; 7; 8; 10; 12; 14; 16; 18. Вес погонного метра арматурных прутков из стекловолокна, представленных на современном рынке, варьируется в пределах 0,02–0,42 кг.
Виды стеклопластиковой арматуры и сферы ее применения
Арматура, для производства которой используется стекловолокно, имеет множество разновидностей, различающихся между собой не только по диаметру и форме профиля (гладкая и с рифлением), но и по области использования. Так, специалисты выделяют стеклопластиковую арматуру:
- рабочую;
- монтажную;
- распределительную;
- специально предназначенную для армирования бетонных конструкций.
В зависимости от решаемых задач такая арматура может использоваться в виде:
- штучных прутков;
- элементов армирующих сеток;
- арматурных каркасов различной конструкции и габаритов.
Арматурная стеклопластиковая сетка 100х100 мм
Несмотря на то, что арматура, изготовленная из стеклопластика, появилась на отечественном рынке недавно, предприятия, строительные компании и частные лица уже достаточно активно используют ее для решения различных задач. Так, набирает популярность применение стеклопластиковой арматуры в строительстве. С ее помощью армируют фундаменты и другие конструкции из бетона (дренажные колодцы, стены и др.), ее применяют для укрепления кладки, выполняемой из кирпича и блочных материалов. Технические характеристики стеклопластиковой арматуры позволяют успешно использовать ее в дорожном строительстве: для армирования дорожного полотна, укрепления насыпей и слабых оснований, создания монолитных бетонных оснований.
Частные лица, самостоятельно занимающиеся строительством у себя на приусадебном участке или на даче, также успели оценить достоинства данного материала. Интересен опыт применения стеклопластиковой арматуры на дачах и в огородах частных домов в качестве дуг для возведения парников. В интернете можно найти множество фото таких аккуратных и надежных конструкций, которые не подвержены коррозии, легко ставятся и так же легко демонтируются.
Каркас самодельного парника из стеклопластиковой арматуры
Большим преимуществом использования такого материала (особенно для частных лиц) является простота его транспортировки. Смотанную в компактную бухту стеклопластиковую арматуру можно увезти даже на легковом автомобиле, чего нельзя сказать об изделиях из металла.
Что лучше – стеклопластик или сталь?
Чтобы ответить на вопрос, какую арматуру лучше использовать – стальную или стеклопластиковую, – следует сравнить основные параметры этих материалов.
- Если арматурные прутки из стали обладают и упругостью, и пластичностью, то стеклопластиковые изделия – только упругостью.
- По пределу прочности стеклопластиковые изделия значительно превосходят металлические: 1300 и 390 МПа соответственно.
- Более предпочтительным является стекловолокно и по коэффициенту теплопроводности: 0,35 Вт/м*С0 – против 46 у стали.
- Плотность арматурных прутков из стали составляет 7850 кг/м3, из стекловолокна – 1900 кг/м3.
- Изделия из стекловолокна, в отличие от арматурных прутков из стали, обладают исключительной коррозионной устойчивостью.
- Стекловолокно – это диэлектрический материал, поэтому изделия из него не проводят электрический ток, отличаются абсолютной прозрачностью для электромагнитных волн, что особенно важно при строительстве сооружений определенного назначения (лаборатории, исследовательские центры и др.).
Между тем изделия из стекловолокна недостаточно хорошо работают на изгиб, что ограничивает их применение для армирования плит перекрытия и других сильно нагруженных бетонных конструкций. Экономическая целесообразность использования арматурных прутков, изготовленных из композитных материалов, заключается еще и в том, что их можно приобрести ровно такое количество, которое вам необходимо, что делает их применение практически безотходным.
Резюмируем все вышесказанное. Даже учитывая все уникальные характеристики композитной арматуры, применять ее следует очень обдуманно и только в тех сферах, где данный материал проявляет себя лучше всего.Нежелательно использовать такую арматуру для укрепления бетонных конструкций, которые в процессе эксплуатации будут испытывать очень серьезные нагрузки, способные стать причиной ее разрушения. Во всех же остальных случаях применение арматуры из стекловолокна и других композитных материалов подтвердило свою эффективность.
Что такое композиты — Откройте для себя композиты
Определение «композит» — это два или более материалов с заметно различающимися физическими или химическими свойствами, классифицируемых как «матрица» или «армирование», объединенных таким образом, чтобы действовать согласованно, все же остаются отдельными и отличными на каком-то уровне, потому что они не полностью сливаются или растворяются друг в друге.
В то время как другие материалы технически являются композитами, этот термин стал обозначать комбинацию смолы и волокнистого армирования, иногда называемую «полимерами, армированными волокном» или композитами FRP. Эта комбинация может производить одни из самых прочных и универсальных материалов для своего веса, которые когда-либо разрабатывались технологиями.
Кроме того, смола, волокно и добавки, входящие в состав композитов, могут быть адаптированы для производства конечных деталей и продуктов с широким диапазоном физических свойств, что позволяет использовать композиты во множестве областей применения.
Хотя смолу, используемую в композитах, иногда называют «пластиком», ее не следует путать с большинством пластиков, которые мы видим сегодня, которые на самом деле представляют собой чистый пластик, такой как игрушки и бутылки из-под газировки.
Композиты обладают уникальными преимуществами по сравнению с традиционными материалами, такими как сталь, алюминий, дерево или бетон. Это связано как с уникальной природой материала, так и с нашей способностью настраивать его компоненты для изменения характеристик конечного продукта. В результате композиты обладают многими выгодными физическими свойствами и большой гибкостью дизайна. Чтобы узнать больше о преимуществах композитов, изучите их применение в различных отраслях:
Преимущества композитов:
- Легкий вес
- Высокая прочность
- Коррозионностойкий
- Высокое соотношение прочности и веса
- Направленная прочность – индивидуальные механические свойства
- Высокая ударопрочность
- Высокая электрическая прочность (изолятор)
- Радар прозрачный
- Немагнитный
- Низкие эксплуатационные расходы
- Быстрая установка
- Долговечность
- Консолидация деталей
- Размерная стабильность
- Геометрия деталей от мелких до крупных – стиль/дизайн – скульптурная форма
- Отделка поверхности по индивидуальному заказу
Композиты открывают целый мир новых возможностей для производителей, дизайнеров и инженеров. Как узнали многие компании, работа с композитами позволяет адаптировать свойства волокон, смол и добавок, чтобы получить именно те свойства материала и рабочие характеристики, которые вам нужны. По мере того, как композитные материалы становились все более сложными, усложнялись и производственные процессы, используемые для изготовления изделий из композитов. Когда-то новые методы, такие как пултрузия, литье под давлением из смолы и крупномасштабная намотка нити, теперь стали основными в индустрии композитов.
Волокнистая арматура , такая как стекло, углерод, арамид или другой армирующий материал, с достаточным отношением длины к толщине для обеспечения заметной армирующей функции в одном или нескольких направлениях.
Узнать больше
Полимерная матричная смола , термопластичная или термореактивная, например полиэфирная, изополиэфирная, винилэфирная, эпоксидная, фенольная.
Узнать больше
Наполнители, добавки, основные материалы добавляют в композиты для контроля процесса формования или улучшения физических свойств конечного продукта (цвет, прочность, долговечность, огнестойкость и многие другие характеристики).
Подробнее
Процессы литья превращают композитные материалы в широкий спектр продуктов и деталей. Ключевой добавкой является катализатор, который инициирует химическую реакцию, в результате которой смола «сшивается» и становится твердой (отвердевающей).
Более эластичная смола или матрица придает форму, защищает волокна и передает нагрузку между волокнами. Волокна, в свою очередь, обеспечивают прочность и жесткость, укрепляя матрицу и помогая ей противостоять трещинам и изломам.
Подробнее
Наука и технология композитных материалов
В таком развитом обществе, как наше, мы все зависим от композитных материалов в некоторых аспектах нашей жизни.
Стекловолокно ГЛОССАРИЙ Стекловолокно Композитный материал, изготовленный из тонких стеклянных волокон, сплетенных в ткань, а затем соединенных синтетическим пластиком или смолой. был разработан в конце 1940-х годов и стал первым современным композитом. Он по-прежнему остается самым распространенным, составляя около 65 процентов всех производимых сегодня композитов. Он используется для изготовления корпусов лодок, досок для серфинга, спортивных товаров, облицовки бассейнов, строительных панелей и кузовов автомобилей. Вы вполне можете использовать что-то из стекловолокна, не подозревая об этом.
Что делает материал композитным
Композитные материалы образуются путем объединения двух или более материалов, обладающих совершенно разными свойствами. Различные материалы работают вместе, чтобы придать композиту уникальные свойства, но внутри композита вы можете легко отличить разные материалы — они не растворяются и не смешиваются друг с другом.
Композиты существуют в природе. Кусок дерева представляет собой композит, состоящий из длинных волокон целлюлозы (очень сложной формы крахмала), скрепленных гораздо более слабым веществом, называемым лигнином. Целлюлоза также содержится в хлопке и льне, но именно связывающая способность лигнина делает кусок древесины намного прочнее пучка хлопковых волокон.
Это не новая идея
Человечество использует композитные материалы тысячи лет. Возьмем, к примеру, глиняные кирпичи. Если вы попытаетесь согнуть лепешку из засохшей грязи, она легко сломается, но будет прочной, если вы попытаетесь раздавить или сжать ее. С другой стороны, кусок соломы обладает большой силой, когда вы пытаетесь его растянуть, но почти не имеет силы, когда вы его смываете. Когда вы смешиваете глину и солому в блоке, свойства двух материалов также объединяются, и вы получаете кирпич, который устойчив как к сжатию, так и к разрыву или изгибу. Говоря более технически, у него есть как хорошие
прочность на сжатие ГЛОССАРИЙ прочность на сжатие Максимальное напряжение, которое может выдержать материал, когда он подвергается нагрузке, которая сжимает его. и хорошо
предел прочности ГЛОССАРИЙ предел прочности при растяжении Максимальное напряжение, которое выдержит материал, когда он подвергается растягивающей нагрузке. .
Еще одним известным композитом является бетон. Здесь заполнитель (мелкие камни или гравий) связан цементом. Бетон обладает хорошей прочностью при сжатии, и его можно сделать более прочным при растяжении, добавив в композит металлические стержни, проволоку, сетку или тросы (таким образом создавая железобетон).
Композиты были изготовлены из формы углерода, называемой графеном, в сочетании с металлической медью, в результате чего получается материал, в 500 раз прочнее, чем медь сама по себе. Точно так же композит графена и никеля имеет прочность, превышающую прочность никеля более чем в 180 раз.
Что касается стекловолокна, то оно изготовлено из
пластик ГЛОССАРИЙ пластик Твердый материал, состоящий из органических полимеров. армированный нитями или стеклянными волокнами. Эти нити можно либо связать вместе и сплести в мат, либо иногда нарезать на короткие отрезки, которые произвольно ориентированы в пластиковой матрице.
Больше, чем просто прочность
В настоящее время многие композиты производятся не только для повышения прочности или других механических свойств, но и для других целей. Многие композиты предназначены для того, чтобы быть хорошими проводниками или изоляторами тепла или обладать определенными магнитными свойствами; свойства, которые являются очень специфическими и специализированными, но также очень важными и полезными. Эти композиты используются в огромном количестве электрических устройств, включая транзисторы, солнечные элементы, датчики, детекторы, диоды и лазеры, а также для изготовления антикоррозионных и антистатических покрытий поверхностей.
Композиты, изготовленные из оксидов металлов, также могут обладать особыми электрическими свойствами и используются для производства кремниевых чипов, которые могут быть меньше и более плотно упакованы в компьютер. Это увеличивает объем памяти и скорость компьютера. Оксидные композиты также используются для создания высокотемпературных сверхпроводящих свойств, которые теперь используются в электрических кабелях.
Изготовление композита
Большинство композитов состоит всего из двух материалов. Один материал (матрица или связующее) окружает и связывает вместе группу волокон или фрагментов гораздо более прочного материала (армирования). В случае сырцовых кирпичей две роли выполняют глина и солома; в бетоне цементом и заполнителем; в куске дерева, целлюлозой и лигнином. В стекловолокне армирование обеспечивается тонкими нитями или волокнами стекла, часто вплетенными в своего рода ткань, а матрица представляет собой пластик.
Примеры различных форм армирования стекла для использования при создании стеклопластика. Источник изображения: Cjp24/Викисклад. Стеклянные нити в стекловолокне очень прочны при растяжении, но они также хрупкие и ломаются при резком изгибе. Матрица не только удерживает волокна вместе, но и защищает их от повреждений, разделяя любые
стресс ГЛОССАРИЙ стресс Сила на единицу площади. Измеряется в тех же единицах, что и давление, а именно в паскалях (Па). Материалы обычно имеют прочность в диапазоне мегапаскалей (МПа) (1 МПа = 1 000 000 Па). среди них. Матрица достаточно мягкая, чтобы ее можно было формировать с помощью инструментов, и ее можно смягчить подходящими растворителями, чтобы можно было произвести ремонт. Любая деформация листа стеклопластика обязательно растягивает часть стеклянных волокон, а они способны этому противостоять, поэтому даже тонкий лист очень прочен. Он также довольно легкий, что является преимуществом во многих приложениях.
За последние десятилетия было разработано много новых композитов, некоторые из которых обладают очень ценными свойствами. Тщательно выбирая армирование, матрицу и производственный процесс, который объединяет их, инженеры могут адаптировать свойства в соответствии с конкретными требованиями. Они могут, например, сделать композитный лист очень прочным в одном направлении, выровняв таким образом волокна, но более слабым в другом направлении, где прочность не так важна. Они также могут выбрать такие свойства, как устойчивость к теплу, химическим веществам и атмосферным воздействиям, выбрав соответствующий матричный материал.
Выбор материалов для матрицы
Для матрицы во многих современных композитах используются термореактивные или термопластичные пластики (также называемые смолами). (Использование пластика в матрице объясняет название «армированный пластик», обычно данное композитам). Пластмассы полимеры ГЛОССАРИЙ полимеры Крупные молекулы, состоящие из множества звеньев (мономеров), связанных друг с другом в цепочку. Существуют природные полимеры (такие как крахмал и ДНК) и синтетические полимеры (такие как нейлон и силикон). которые скрепляют арматуру и помогают определить физические свойства конечного продукта.
Термореактивные пластмассы жидкие при приготовлении, но затвердевают и становятся жесткими (т.е. отверждаются) при нагревании. Процесс схватывания необратим, поэтому эти материалы не становятся мягкими при высоких температурах. Эти пластмассы также устойчивы к износу и воздействию химических веществ, что делает их очень прочными даже в экстремальных условиях.
Термопластические пластмассы, как следует из названия, являются твердыми при низких температурах, но размягчаются при нагревании. Хотя они используются реже, чем термореактивные пластмассы, у них есть некоторые преимущества, такие как более высокая вязкость разрушения, длительный срок хранения сырья, способность к переработке и более чистое и безопасное рабочее место, поскольку для процесса отверждения не требуются органические растворители.
Керамика, углерод и металлы используются в качестве матрицы для некоторых узкоспециализированных целей. Например, керамика используется, когда материал будет подвергаться воздействию высоких температур (например, теплообменники), а углерод используется для продуктов, подверженных трению и износу (например, подшипники и шестерни).
Электронно-микроскопическое изображение в искусственном цвете композита с магниевой матрицей, армированного титана-алюминиевым карбидом.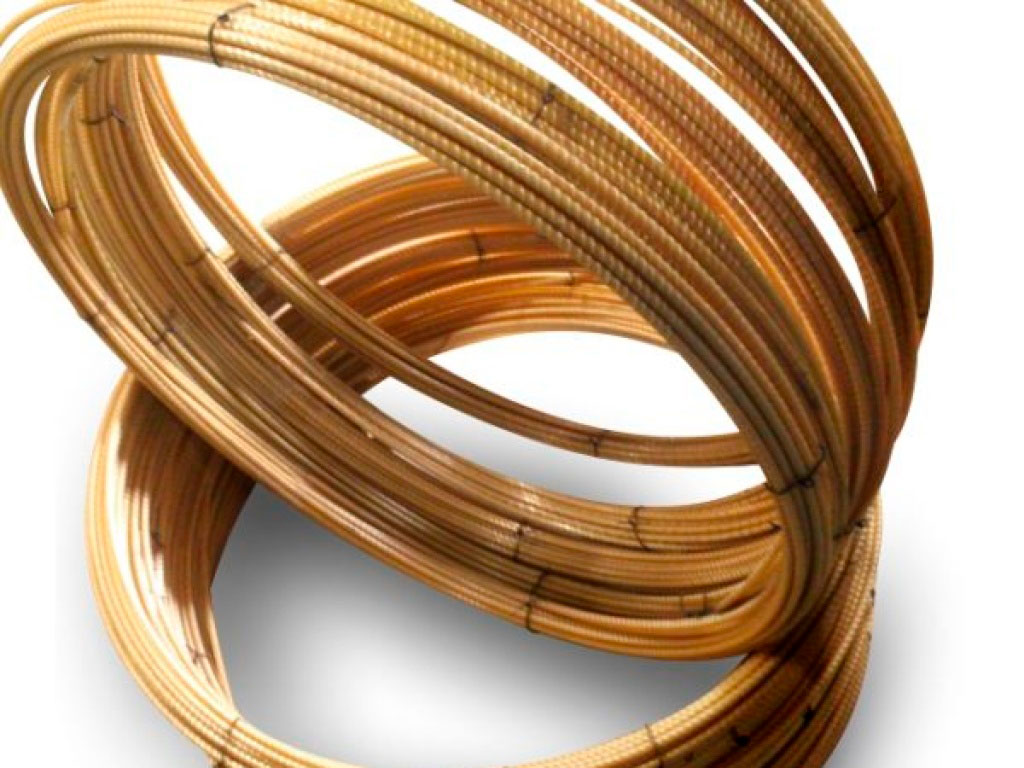
Выбор материалов для армирования
Хотя стекловолокно является наиболее распространенным армирующим материалом, во многих передовых композитах теперь используются тонкие волокна из чистого углерода. Можно использовать два основных типа углерода — графит и углеродные нанотрубки. Оба они представляют собой чистый углерод, но атомы углерода расположены в разных кристаллических конфигурациях. Графит — очень мягкое вещество (используется в «графитовых» карандашах) и состоит из листов атомов углерода, расположенных в виде шестиугольников. Связи, скрепляющие шестиугольники вместе, очень прочные, но связи, скрепляющие листы шестиугольников, довольно слабые, что и делает графит мягким. Углеродные нанотрубки изготавливаются путем скручивания одного листа графита (известного как графен) в трубку. Получается чрезвычайно прочная конструкция. Также возможно иметь трубки, состоящие из нескольких цилиндров — трубки внутри трубок.
Композиты из углеродного волокна легче и намного прочнее стекловолокна, но и дороже. Из этих двух графитовые волокна дешевле и проще в производстве, чем углеродные нанотрубки. Они используются в конструкциях самолетов и высокоэффективном спортивном оборудовании, таком как клюшки для гольфа, теннисные ракетки и гребные лодки, и все чаще используются вместо металлов для ремонта или замены поврежденных костей.
Нити из бора еще прочнее (и дороже), чем углеродные волокна. Нанотрубки из нитрида бора имеют дополнительное преимущество, заключающееся в том, что они намного более устойчивы к теплу, чем углеродные волокна. Они также обладают пьезоэлектрическими свойствами, что означает, что они могут генерировать электричество при воздействии на них физического давления, такого как скручивание или растяжение.
Полимеры также могут использоваться в качестве армирующего материала в композитах. Например, кевлар, изначально разработанный для замены стали в радиальных шинах, но наиболее известный своим использованием в пуленепробиваемых жилетах и шлемах, представляет собой полимерное волокно, обладающее чрезвычайной прочностью и повышающее ударную вязкость композита. Применяется в качестве армирования в композитных изделиях, требующих легкой и надежной конструкции (например, конструкционные детали корпуса самолета). Еще более прочным, чем кевлар, является вещество, изготовленное из комбинации графена и углеродных нанотрубок.
Источник: NASA Goddard/YouTube. Посмотреть детали видео и расшифровку.
Выбор производственного процесса
Изготовление объекта из композитного материала обычно включает в себя некоторую форму формы. Армирующий материал сначала помещается в форму, а затем напыляется или закачивается полужидкий матричный материал для формирования объекта. Можно приложить давление, чтобы вытеснить любые пузырьки воздуха, а затем форму нагреть, чтобы матрица затвердела.
Процесс формовки часто выполняется вручную, но автоматическая обработка на машинах становится все более распространенной. Один из этих методов называется
пултрузия ГЛОССАРИЙ пултрузия Непрерывный процесс формования, при котором длинные армирующие пряди механически выравниваются для композитного материала, а затем пропускаются через ванну с термореактивной смолой. Затем нити с покрытием собираются с помощью механической направляющей перед процессом отверждения. (термин, образованный от слов «тянуть» и «экструзия»). Этот процесс идеально подходит для изготовления прямых изделий с постоянным поперечным сечением, таких как мостовые балки.
Во многих тонких конструкциях сложной формы, таких как изогнутые панели, композитная структура строится путем наложения листов тканого волокнистого армирования, пропитанных пластиковым матричным материалом, на базовую форму соответствующей формы. Когда панель изготовлена до необходимой толщины, матричный материал отверждается.
Сэндвич-композиты
Многие новые типы композитов производятся не методом матрицы и армирования, а путем укладки нескольких слоев материала. Структура многих композитов (например, используемых в панелях крыльев и корпусов самолетов) состоит из сот из пластика, зажатых между двумя обшивками из композитного материала, армированного углеродным волокном.
Сэндвич-структура из сотового композита от НАСА.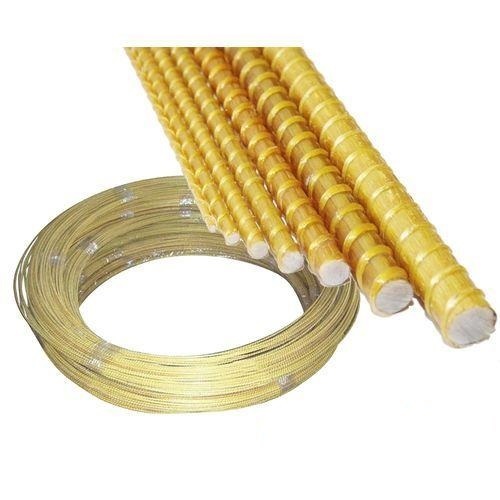
Эти сэндвич-композиты сочетают в себе высокую прочность и особенно жесткость на изгиб с малым весом. Другие методы включают простое наложение нескольких чередующихся слоев различных веществ (например, графена и металла) для получения композита.
Зачем использовать композиты?
Самым большим преимуществом композитных материалов является прочность и жесткость в сочетании с легкостью. Выбирая подходящую комбинацию армирующего и матричного материала, производители могут добиться свойств, точно соответствующих требованиям к конкретной конструкции для конкретной цели.
- Композиты в Австралии
Австралия, как и все развитые страны, проявляет большой интерес к композитным материалам, которые многие считают «материалами будущего». Основная задача состоит в том, чтобы снизить затраты, чтобы композиты можно было использовать в продуктах и приложениях, которые в настоящее время не оправдывают затрат. В то же время исследователи хотят улучшить характеристики композитов, например, сделать их более устойчивыми к ударам.
Один из новых методов включает «текстильные композиты». Вместо того, чтобы укладывать армирующие волокна по отдельности, что медленно и дорого, их можно связать или сплести вместе, чтобы сделать своего рода ткань. Это может быть даже трехмерным, а не плоским. Пространства между текстильными волокнами и вокруг них затем заполняются матричным материалом (например, смолой) для изготовления изделия.
Этот процесс можно легко выполнить с помощью машин, а не вручную, что делает его быстрее и дешевле. Соединение всех волокон вместе также означает, что композит с меньшей вероятностью будет поврежден при ударе.
В связи со снижением затрат другие варианты использования композитов становятся все более привлекательными. При изготовлении корпусов и надстроек лодок из композитов используется их устойчивость к коррозии. У минных охотников ВМС Австралии композитный корпус, поскольку магнитный эффект стального корпуса будет мешать обнаружению мин.
Также в разработке находятся вагоны для поездов, трамваев и других «движущихся людей», изготовленных из композитных материалов, а не из стали или алюминия.
Здесь привлекательность заключается в легкости композитов, поскольку в этом случае транспортные средства потребляют меньше энергии. По той же причине мы будем видеть все больше и больше композитов в автомобилях в будущем.
Ярким примером является современная авиация, как военная, так и гражданская. Без композитов было бы гораздо менее эффективно. Фактически, потребность этой отрасли в легких и прочных материалах была главной движущей силой разработки композитов. В настоящее время часто можно встретить секции крыла и хвостового оперения, пропеллеры и лопасти несущего винта, изготовленные из передовых композитов, а также большую часть внутренней конструкции и фурнитуры. Планеры некоторых небольших самолетов полностью сделаны из композитных материалов, как и крылья, хвостовое оперение и панели корпуса больших коммерческих самолетов.
Размышляя о самолетах, стоит помнить, что композиты менее склонны к полному разрушению под нагрузкой, чем металлы (например, алюминий). Небольшая трещина в куске металла может очень быстро распространиться с очень серьезными последствиями (особенно в случае с самолетом). Волокна в композите блокируют расширение любой небольшой трещины и распределяют напряжение вокруг.
Подходящие композиты также хорошо противостоят нагреву и коррозии. Это делает их идеальными для использования в продуктах, которые подвергаются воздействию экстремальных условий, таких как лодки, оборудование для обработки химикатов и космические корабли. В целом композитные материалы очень прочны.
Еще одним преимуществом композитных материалов является то, что они обеспечивают гибкость конструкции. Композитным материалам можно придавать сложные формы, что очень удобно при производстве чего-то вроде доски для серфинга или корпуса лодки.
Кроме того, большая работа в настоящее время направлена на разработку композитных материалов, изготовленных из отходов, таких как сельскохозяйственные отходы, строительные материалы или пластиковые контейнеры для напитков.