Кованые изделия. Изготовление кованых изделий.
Одним из видов обработки металла является художественная ковка, известная с давних времён. Она стала использоваться несколько столетий назад и до сих пор сохраняет свою актуальность. Великолепные кованые изделия особенно ценились и были на пике востребованности в позднее средневековье. Они являлись настоящим украшением экстерьера особняков и интерьера внутренних покоев знатных особ.
Специалисты, использующие секреты ковки при изготовлении предметов различного назначения, были истинными мастерами художественного творчества. Благодаря их таланту и дизайнерским идеям на свет появились отменные по качеству и внешнему виду кованые изделия — настоящие шедевры искусства, которые представляют собой достаточно прочные элементы и обладают длительным сроком эксплуатации.
Кованые перила
Кованые ворота
Кованый козырек
Используемые виды ковки
Для придания металлическому шедевру задуманной формы соблюдают определённый температурный режим. Используют два основных метода, принципиально отличающихся друг от друга:
- Холодная ковка. Делаются предварительные заготовки. Созданное таким образом изделие по своему виду не является эксклюзивным и не обладает индивидуальными особенностями. Применяется для выпуска крупных и стандартных элементов конструкций, среди которых кованые ворота, беседки, козырьки над входом и много других предметов, не требующие тонкой работы.
- Горячая ковка. Представляет собой классический вид обработки металла с использованием ручного труда. Результатом является эксклюзивное кованое изделие, не имеющее точных аналогов. К обработке приступают только при достижении определённого температурного режима согласно технологии.
Производство кованых изделий в компании «СталИван»
Богатый ассортимент превосходного по качеству и прочности товара представлен на продажу в нашем магазине кованых изделий. Покупатель не только может приобрести уже готовые предметы по каталогу, но и сделать их индивидуальный заказ. Для более детального ознакомления с каждым видом товара представлены фото. Специалисты компании берут за основу не только свои эскизы, но и выполняют заказы по рисункам, предоставленными будущими покупателями. Одним из направлений работы является производство различного рода аксессуаров из металла. Богатый опыт и отличные знания позволяют нашим мастерам выпускать кованые изделия различного предназначения и отличного качества.
Кованая цветочница на окно
Кованое ограждение для балкона
Кованый навес
Отличительной особенностью нашего магазина является правильное соотношение цены и качества. Выбирая из каталога любой товар, покупатель приобретает оригинальное в привлекательном внешнем оформлении изделие. При оформлении интерьера квартиры, либо дома добиться необычного стиля можно с помощью кованых элементов из металла. Для этого стоит лишь заказать в нашем магазине подходящий вариант. Наши менеджеры помогут вам определиться с выбором, учитывая нюансы конкретного помещения или ландшафтного участка. К покупке недешевых предметов ковки нужно подходить максимально ответственно, дабы не разочароваться в последствии в опрометчиво совершенном приобретении.
Производством в нашей компании занимаются квалифицированные мастера, которым хорошо известны тонкости работы с различными сплавами. Мы гарантируем, что готовая кованая конструкция приятно удивит вас:
Своей функциональностью
Утонченностью форм
Безупречным продолжительным сроком службы
Устойчивостью к воздействию внешних факторов
Персональный подход к каждому клиенту, соблюдение условий технологического процесса, талантливые сотрудники — то, что выгодно выделяет нашу мастерскую ковки среди конкурентов.
Изготовление кованых изделий на заказ в Самаре
Кованые изделия: заборы, калитки, решетки, ограждения, лестницы и перила
Технология ручной ковки позволяет создавать огромное разнообразие индивидуальных изделий с уникальным оформлением. Металл много лет пользуется популярностью для изготовления различных конструкций за счет сочетания оптимальных технических характеристик. При этом кованые изделия, малые архитектурные формы любого назначения, оригинальные художественные элементы неповторимо дополнят интерьер и экстерьер любых зданий, загородных территорий.
Фабрика художественной ковки разрабатывает проекты по идеям, которые предлагает Заказчик. Профессиональные кузнецы и квалифицированные дизайнеры готовы выполнить самые смелые предложения с учетом технологических возможностей. Для опытных специалистов Фабрики не существует практически никаких ограничений – мы воплощаем в единственном экземпляре нестандартные интерьерные решения с особым колоритом. Каждое изделие отличается не только долговечностью и функциональностью, но и уникально по своему художественному исполнению.
Большой выбор кованых элементов и конструкций
На Фабрике художественной ковки можно заказать изготовление разнообразных изделий и атрибутики из металла:
- кованые заборы и калитки, ворота (распашные и откатные),
- ограждения и перила,
- кованые решетки в Самаре для любых объектов и назначения, в том числе на окна и балконы,
- защитные козырьки и навесы,
- лестницы винтовые и с перилами «под ключ»,
- кованые аксессуары, принадлежности, декоративные украшения для каминов,
- кованые дымники (колпаки на дымоход),
- ритуальные ограды,
- мангалы и интересные элементы, дополняющие гриль-зону,
- оригинальные кованые элементы и предметы интерьера – лавочки, беседки, вешалки, подсвечники, светильники, подковы, цветы, подставки для цветов и т.
Любые дизайнерские задумки и Hand-Made сувениры мы выполним качественно и в согласованные сроки. У нас оформляют заказы и для себя лично, и для оформления подарка родным, друзьям, коллегам.
Кованые элементы отлично дополняют ландшафтный дизайн участка и разграниченных зон. Кованая мебель и декоративные сувениры стильно украшают не только загородные дома, но и просторные городские квартиры. Такое оформление интерьеров и экстерьеров востребовано для самых разных по функционалу объектов благодаря таким преимуществам:
- изысканный внешний вид кованых элементов – плавные линии, изгибы придают легкость и воздушность готовым конструкциям,
- ручная работа позволяет создать уникальные вещи в единственном экземпляре,
- художественная ковка помогает выделить главные акценты в различных стилях дизайна, подчеркнуть неповторимость идеи Заказчика.
Как производят поковки | Ассоциация кузнечной промышленности
Ковка — придание формы металлу пластической деформацией — охватывает множество видов оборудования и методов. Знание различных операций ковки и характерного течения металла, производимого каждой из них, является ключом к пониманию конструкции ковки.
Ковка с помощью молота и пресса
Как правило, кованые компоненты формуются молотком или прессом. Ковка на молоте осуществляется последовательным оттиском штампа с использованием повторяющихся ударов. Качество ковки, а также экономичность и производительность молоткового процесса зависят от инструментов и навыков оператора. Появление программируемых молотков привело к меньшей зависимости от оператора и повышению согласованности процесса. В прессе заготовка обычно ударяется только один раз в каждом оттиске штампа, и дизайн каждого оттиска становится более важным, а навыки оператора менее важны.
Рис. 1. Сжатие между узкими штампами. |
Ковка в открытых штампах Ковка в открытых штампах с использованием молотов и прессов — это современное расширение доиндустриального кузнечного дела, работающего с молотом на наковальне.
При открытой штамповке заготовка не полностью ограничена, так как она формуется штампами. Процесс с открытым штампом обычно связан с большими деталями, такими как валы, втулки и диски, но вес деталей может варьироваться от 5 до 500 000 фунтов.
Большинство открытых штамповок производится на плоских штампах. Круглые обжимные штампы и V-образные штампы также используются парами или с плоскими штампами. Операции, выполняемые на прессах с открытой матрицей, включают:
- Вытягивание или уменьшение поперечного сечения слитка или заготовки для их удлинения.
- Осадка или уменьшение длины слитка или заготовки до большего диаметра.
- Осадка, вытяжка и прошивка — процессы, иногда совмещенные с ковкой на оправке для ковки колец грубой формы.
|
По мере того, как поковочная заготовка штампуется или прессуется, она многократно перемещается между штампами, пока не достигнет окончательных размеров поковки. Поскольку этот процесс является неточным и требует значительных навыков мастера по ковке, сохраняются значительные припуски на заготовку для компенсации неровностей ковки. Кованая деталь подвергается черновой обработке, а затем чистовой обработке до окончательных размеров. Все более широкое использование средств управления прессом и молотом делает ковку в открытых штампах и все процессы ковки в этом отношении более автоматизированными.
При свободной штамповке металлы обрабатываются при температурах, превышающих их температуры рекристаллизации. Поскольку процесс требует многократного изменения положения заготовки, заготовка охлаждается во время ковки в открытых штампах ниже температуры горячей обработки или рекристаллизации. Затем его необходимо повторно нагреть, прежде чем можно будет продолжить ковку. Например, стальной вал диаметром 2 фута и длиной 24 фута может потребовать от четырех до шести плавок, прежде чем будут достигнуты окончательные размеры штамповки.
При ковке стали в открытых штампах эмпирическое правило гласит, что на каждый квадратный дюйм поперечного сечения заготовки требуется 50 фунтов падающего веса.
Рис. 3. Поковка валков с использованием валков специальной формы. |
Сжатие между плоскими штампами или осадка — это процесс ковки в открытых штампах, при котором продолговатая заготовка помещается торцом на нижний штамп, а ее высота уменьшается за счет движения вниз верхнего штампа. Трение между торцами заготовки и штампами препятствует свободному поперечному растеканию металла, что приводит к типичной бочкообразной форме. Контакт с холодной поверхностью штампа охлаждает торцы металла, повышая его сопротивление деформации и усиливая бочкообразность.
Осадка между параллельными плоскими штампами ограничена деформацией, симметричной относительно вертикальной оси.
Более узкая матрица лучше удлиняется, но слишком узкая матрица будет резать металл, а не удлинять. На направление потока материала также можно влиять, используя фильеры с поверхностями особой формы.
Сжатие между узкими штампами является прерывистым, так как необходимо выполнить много ходов, пока заготовка перемещается в осевом направлении. Эту задачу можно сделать непрерывной путем прокатки ковкой (рис. 2). Обратите внимание на сходство между рис. 1 и рис. 2. Ширина матрицы теперь представлена длиной дуги контакта. Достигаемое удлинение зависит от длины этой контактной дуги.
Рис. 4. Штамповка |
Ролики большего размера вызывают большее поперечное расхождение и меньшее удлинение из-за большей разницы трения в дуге контакта, тогда как валки меньшего размера больше удлиняются. Боковой разброс можно уменьшить, а удлинение увеличить, используя валки специальной формы (рис. 3).
Свойства кованых деталей очень удовлетворительные. В большинстве случаев облоя нет, а структура волокна очень благоприятная и непрерывная на всех участках. Валки выполняют определенное удаление накипи, делая поверхность продукта гладкой и без накипных карманов.
Ковка штампов
В самом простом примере ковки штампов, на который приходится большая часть производства ковки, два штампа соединяются вместе, и заготовка подвергается пластической деформации до тех пор, пока ее увеличенные стороны не коснутся боковых стенок штампа
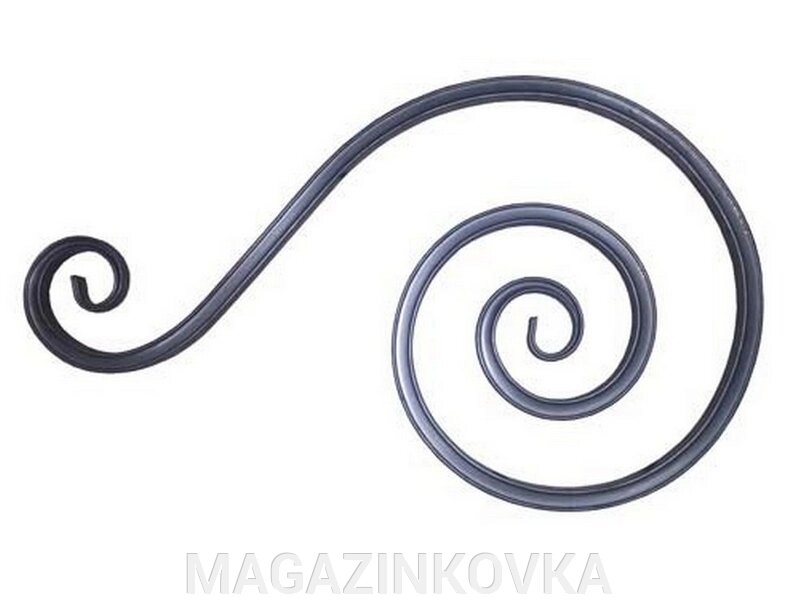
Штампованные поковки могут быть изготовлены на горизонтально-ковочной машине (высадочной машине) в процессе, называемом высадка . При осадке заготовка удерживается между неподвижной и подвижной матрицей, в то время как горизонтальный пуансон создает давление для ковки заготовки (рис. 5). После каждого хода плашки с несколькими тиснениями могут открываться, позволяя перемещать припуск из одной полости в другую.
Рис. 5. Осадка. |
Форма поковки в штампах, штамповка в закрытых штампах не зависит от формирования облоя для достижения полного заполнения штампа. Материал деформируется в полости, которая практически не допускает выхода лишнего материала, что предъявляет повышенные требования к конструкции штампа.
Для ковки штамповкой штампы становятся более важными, а уровень квалификации оператора менее критичен при операциях ковки штамповкой. Последовательность штамповки на прессе обычно состоит из блока и чистовой обработки, иногда с преформой, прожигом или обрезкой. Деталь обычно попадает только один раз в каждую полость штампа.
Преимущество прецизионной ковки Решение о применении методов прецизионной ковки зависит от относительной экономичности дополнительных операций и инструментов по сравнению с отказом от механической обработки. |
Этапы процесса прокатки колец | |
. | |
2 | 3 |
4 | 5 |
6 | 7
|
Прокатка колец
Прокатка колец превратилась из искусства в строго контролируемый технологический процесс. Бесшовные катаные кольца производятся на различном оборудовании. Все они дают один и тот же продукт — бесшовное сечение с ориентацией волокон по окружности. Эти кольца обычно обладают тангенциальной прочностью и пластичностью и часто менее дороги в производстве, чем аналогичные поковки в закрытых штампах. Таким образом, процесс кольцевой прокатки обеспечивает однородный окружной поток зерна, простоту изготовления и универсальность в отношении материала, размера, массы и геометрии.
В процессе прокатки колец заготовку нагревают до температуры ковки и помещают на натяжной (внутренний) валок прокатной машины. Давление на стенку оказывает основной (внешний) валок при вращении кольца. Площадь поперечного сечения уменьшается по мере увеличения внутреннего и внешнего диаметров. Оборудование может быть полностью автоматизировано, начиная с нагрева заготовки и заканчивая послекузовной обработкой. Усовершенствованное оборудование для прокатки колец может прокатывать контуры как по внутреннему, так и по внешнему диаметру кольца, что позволяет добиться значительного снижения веса, экономии материалов и снижения затрат на механическую обработку.
Существует бесконечное множество размеров, до которых можно прокатывать кольца, начиная от втулок подшипников качения и заканчивая кольцами диаметром 25 футов и высотой лицевой поверхности более 80 дюймов. Различные профили могут быть прокатаны за счет соответствующей формы ведущих и холостых валков.
Экструзия При экструзии (рис. 6) заготовка помещается в контейнер и сжимается до тех пор, пока давление внутри металла не достигнет уровня текучести. Заготовка полностью заполняет емкость, а дополнительное давление заставляет ее проходить через отверстие и формировать экструдированный продукт.
Экструзия может быть прямой (прямой) или обратной (реверсивной), в зависимости от направления движения между пуансоном и экструдируемым продуктом. Прессованное изделие может быть сплошным или полым. Экструзия труб типична для прямой экструзии полых форм, а обратная экструзия используется для массового производства контейнеров.
|
Прошивка близка к обратному выдавливанию, но отличается большим перемещением пуансона по отношению к движению материала заготовки.
Вторичные процессы Помимо основных процессов ковки, часто используются вторичные операции. Волочение через штамп — это удобный способ устранения кованой тяги (рис. 7а). Форма деформации – тангенциальное сжатие. Диаметр волочильного кольца может быть немного меньше внешнего диаметра предварительно кованой оболочки для контроля или уменьшения толщины стенки и увеличения высоты оболочки на чертеже или глажение операция (рис. 7b).
Гибка может выполняться на готовой поковке или на любом этапе ее изготовления.
Поскольку поковочная заготовка может принимать сложную форму, редко требуется только один оттиск штампа. Более желательным может быть предварительное формование заготовки для поковки путем ее сгибания или прокатки или обработки в предварительном штампе. Повышение производительности, срока службы штампа и качества ковки часто перевешивает тот факт, что предварительное формование увеличивает операцию и сопутствующие расходы. Ковка в одном последнем оттиске штампа может быть практичной для очень малых тиражей деталей.
|
Поскольку для гибки крупных деталей требуется машина с длинным ходом, часто необходимы специальные механические или гидравлические прессы. Простые формы можно согнуть за одну операцию, а более сложные контуры выполняются последовательно. Если сложные формы должны быть сформированы за одну операцию, инструмент должен содержать подвижные элементы.
Специальные методы После деформации кованые детали могут подвергаться дальнейшей металлообработке. Заусенец удаляется, могут потребоваться перфорированные отверстия, может потребоваться улучшенная обработка поверхности или более высокая точность размеров.
Обрезка — Заусенец обрезается до того, как поковка будет готова к отправке. Иногда, особенно в случае сплавов, чувствительных к растрескиванию, это может быть выполнено шлифовкой, фрезерованием, распиловкой или газовой резкой.
Чеканка— Чеканка и глажка по существу представляют собой операции по калибровке с применением давления к критическим поверхностям для улучшения допусков, сглаживания поверхностей или устранения сквозняков.
Чеканка обычно выполняется на поверхностях, параллельных линии разъема, в то время как глажение характеризуется продавливанием чашеобразного компонента через кольцо до размера по внешнему диаметру. В обеих операциях задействован небольшой поток металла, и облоя не образуется.
Обжим — Эта операция связана с процессом ковки в открытых штампах, при котором заготовка вытягивается между плоскими узкими штампами. Но вместо приклада вращается молоток, производящий несколько ударов, иногда до 2000 ударов в минуту. Это полезный метод первичной обработки, хотя в промышленном производстве его роль обычно заключается в отделке. Обжатие может быть остановлено в любой точке по длине заготовки и часто используется для заострения концов труб и стержней, а также для изготовления ступенчатых колонн и валов уменьшающегося диаметра.
|
Горячее выдавливание — Выдавливание наиболее подходит для формования деталей с резко изменяющимся поперечным сечением и, следовательно, является прямым конкурентом непрерывной осадке и горизонтально-ковочной машине. На рис. 8 секция стержня тщательно контролируемого объема нагревается, очищается от окалины и помещается в головку. Под давлением плотно прилегающего пуансона (рис. 8а) материал сначала заполняет полость, затем часть его выдавливается в длинный стержень. В конце хода (рис. 8б) получается гидроблок, нуждающийся только в шлифовке посадочных поверхностей.
Существует несколько вариантов процесса экструзии, многие из них запатентованы. Заготовка может быть полой (обработанной), прошитой на отдельной операции или в самом процессе экструзии. Во всех случаях качество нагрева, эффективность удаления или предотвращения образования накипи, а также эффективность смазки имеют первостепенное значение. Разнообразие производимых форм многочисленно. Точность размеров, качество поверхности и производительность высоки, и за одну операцию можно достичь большей степени деформации, чем при любом другом методе ковки.
Холодная, теплая и горячая ковка – в чем разница? Холодная ковка Теплая ковка Горячая |
Вернуться к началу
Ковка и кованые детали
Хотя ковка является одним из старейших методов обработки металлов, он остается одним из самых эффективных и по сей день. По своей сути ковка представляет собой процесс формования необработанного металла без полного расплавления материала. Металл остается в твердом состоянии, пока оператор выполняет любую комбинацию методов формования, таких как ковка, прокатка или прессование. Хотя существует множество вариантов ковки, каждый из которых имеет свои явные преимущества, большинство из них включает нагрев заготовки до очень высоких температур для облегчения процессов формообразования.
По сравнению с литьем или другими методами металлообработки ковка обеспечивает наиболее желательные физические характеристики, включая очень высокую степень прочности на растяжение, по привлекательной цене. Эти полезные свойства в первую очередь связаны с изменениями в зернистости металла. Поскольку материал никогда не плавится, ударные или сжимающие силы, прилагаемые во время ковки, заставляют зерна следовать за потоком готового продукта. Это создает компоненты, которые намного прочнее, чем их механически обработанные и литые аналоги.
Cornell Forge делает эти преимущества доступными для клиентов из разных отраслей, предлагая полный спектр квалифицированных услуг по ковке, отвечающих потребностям множества приложений.
Процесс ковки
Существует множество подтипов более широкого процесса ковки, поэтому точные этапы формирования изделия могут различаться. Однако большинство процедур будет следовать одной и той же общей схеме.
- Ковка основана на использовании штампов для сжатия и придания формы металлу, поэтому очень важно определить, какой набор инструментов будет наиболее эффективным для достижения желаемой формы. Во многих случаях потребуется индивидуальная конструкция штампа, чтобы конечный продукт точно соответствовал ожиданиям.
Для более крупных производственных циклов этот шаг может включать проектирование и изготовление нескольких штампов, предназначенных для правки, формовки или резки.
- После завершения планирования и изготовления инструментов можно приступать к собственно металлообработке. Во-первых, заготовку или заготовку необходимо разрезать по размеру. После резки его необходимо нагреть до нужной температуры. После нагрева заготовка готова к формованию.
- На этом этапе различные методы ковки начинают расходиться. В зависимости от выбранного процесса заготовку можно нагреть и запрессовать между двумя штампами или вставить в формованную полость и спрессовать. В некоторых случаях оператор оставляет заготовку при комнатной температуре и обрабатывает ее вручную молотками в процессе, называемом холодной ковкой.
- Наконец, могут быть некоторые необходимые завершающие процедуры. Например, некоторые штампы будут производить заусенцы, которые необходимо обрезать.
Узнайте о различных процессах ковки.
В Cornell Forge мы тщательно работаем над тем, чтобы свести к минимуму потребность во второстепенных процедурах, чтобы мы могли передать эту экономию нашим клиентам. Выбор метода ковки зависит от формируемой детали. Мы работаем с каждым клиентом, чтобы выбрать метод, который обеспечит точные, последовательные результаты и соответствующие физические свойства для его случая использования.
Преимущества ковки
Большинство компонентов, которые можно изготовить с помощью ковки, вместо этого можно отлить. Однако кованые изделия обладают значительными преимуществами по сравнению с деталями, изготовленными методом литья, особенно в тех случаях, когда прочность и долговечность имеют первостепенное значение. Это связано с тем, что ковка коренным образом изменяет структуру металла — при сжатии твердого или нагретого металла материал подвергается металлургической рекристаллизации, что является полезным перераспределением зерна металла.
После рекристаллизации кованые детали обладают гораздо более высокой ударной вязкостью и прочностью на сдвиг, чем сырой или литой материал. В качестве дополнительного преимущества эти улучшения прочности могут быть настолько выраженными, что они противодействуют необходимости использования дорогих сплавов для достижения желаемой прочности.
Ознакомьтесь с различными продуктами, которые мы производим.
Дополнительные преимущества ковки:
- Прочность на растяжение . Исследование Университета Толедо показало, что кованые детали обладают на 26% более высокой прочностью на растяжение, чем сопоставимые чугунные детали. В результате кованые компоненты могут выдерживать значительно большее растяжение без разрыва, чем другие детали.
- Усталостная прочность . Кованые компоненты обладают явно более высокой усталостной прочностью, что обеспечивает более длительный срок службы по сравнению с компонентами, изготовленными другими методами, при наблюдении в тех же тяжелых условиях эксплуатации.
- Универсальность . Как ковка, так и литье могут производить широкий спектр больших и малых изделий.
Редко есть причина предпочесть литье ковке только для того, чтобы получить другую форму.
- Однородность . По сравнению с литыми деталями кованые имеют более однородный состав и структуру, что способствует их внушительному сроку службы.
Помимо превосходства литья по этим ключевым показателям, ковка также предотвращает распространенные дефекты, встречающиеся в литых деталях. При литье некоторый процент конечных деталей обычно имеет неприемлемый уровень пористости, усадки или даже пустот. Такие проблемы часто могут приводить к тому, что приходится сбрасывать вблизи полностью обработанных литых деталей, что приводит к потере ценного времени обработки. Ни одна из этих проблем не может возникнуть при ковке, потому что материал никогда не расплавляется и не преобразуется.
Постоянное качество является значительным преимуществом, особенно с точки зрения стоимости. Если литая деталь имеет пористость, ее необходимо утилизировать и отлить заново, что влечет за собой значительные материальные и трудовые затраты. Ковка полностью снижает этот риск. Кованые детали также обеспечивают долгосрочную экономию средств из-за их долговечности, уменьшая частоту выхода компонентов из строя и необходимости их замены.
В целом кованые детали более прочные, чем аналогичные по цене аналоги, и поэтому являются отличным вариантом для многих промышленных компонентов.
Промышленное применение
Многие отрасли промышленности начали признавать ключевые преимущества кованых компонентов. К ним относятся:
- Аэрокосмическая отрасль . Авиационные двигатели, компоненты шасси и аналогичные аэрокосмические детали выигрывают от долговечности и амортизации, обеспечиваемых кованым металлом.
- Автомобиль . Двигатели, рамы и трансмиссии — все это примеры компонентов, которые часто выковываются, чтобы использовать преимущества более высокой прочности, сопротивления и амортизирующих свойств кованого металла.
- Морской и железнодорожный .
Детали, предназначенные для строительства и ремонта лодок или рельсов, часто выковываются, чтобы обеспечить долговечность при больших напряжениях в суровых условиях эксплуатации.
- Ручные и промышленные инструменты . Инструменты должны выдерживать большую ударную силу без деформации или растрескивания. Кованый металл обеспечивает долговечность, которую трудно достичь с помощью литья.
- Клапаны высокого давления и фитинги . Существует потребность в чрезвычайно прочных фитингах и клапанах для приложений высокого давления, которые охватывают многие отрасли. Кованые компоненты часто предпочтительнее из-за их прочности и долговечности в суровых условиях или при высоких давлениях.
- Машины и оборудование для нефтяных месторождений . Нефтяная и газовая промышленность предъявляет уникальные требования к оборудованию, и отказы могут быть чрезвычайно дорогостоящими. Кованый металл безопаснее и снижает потребность в дорогостоящих остановах для замены вышедших из строя деталей.
- Строительство, обработка материалов и добыча полезных ископаемых . Строительные площадки, шахты и погрузочно-разгрузочные работы часто подвергают оборудование очень большим нагрузкам и жестким условиям эксплуатации. Кованые компоненты часто предпочтительнее для защиты от опасных неисправностей и ненужных простоев.
В целом причины роста популярности ковки понятны. Это рентабельно и приводит к созданию прочных, высокопроизводительных компонентов, устойчивых к износу даже в самых сложных условиях эксплуатации. Эти преимущества могут быть усилены за счет тщательного выбора материалов, поэтому Cornell Forge работает в основном с высокопрочными сплавами, а также с нержавеющей сталью, которые обеспечивают максимальную прочность, долговечность и коррозионную стойкость.
Запросите кованые изделия на заказ в Cornell Forge сегодня
Компания Cornell Forge обладает более чем 90-летним опытом в области ковки, и мы используем этот опыт, чтобы направлять наших клиентов на каждом этапе процесса ковки. Мы предлагаем помощь в проектировании, консультации и услуги по оптимизации, а затем собственное производство инструментов, что позволяет нам работать с клиентами с самого начала планирования продукта. Наши разнообразные предложения позволяют нам работать в различных отраслях промышленности со сложными потребностями, включая военную, медицинскую и аэрокосмическую отрасли.
Как компания, сертифицированная по стандарту ISO 9001:2015, мы придерживаемся строгих стандартов качества, включая строгие меры контроля процесса, чтобы гарантировать, что каждая кованая деталь соответствует ожиданиям. Более того, мы работаем с сетчатыми или почти сеточными процессами ковки, чтобы уменьшить количество отходов и сократить время выполнения заказа, а это означает, что вам не нужно жертвовать устойчивостью ради эффективности.
Наши возможности включают ковку нержавеющей стали и стальных сплавов, а также дополнительные услуги, начиная от термообработки и заканчивая сборкой и испытаниями.