Художественная холодная ковка металла — Производство станков для художественной ковки.
Художественная холодная ковка металлов – это придание нужной формы металлическим прокатам различного сечения без предварительного нагрева рабочего материала. По месту целевого использования готовых изделий, полученных методом художественной холодной ковки металла, этот метод подразделяется на:
- Интерьерную ковку. То есть внутридомовую. Это когда готовые изделия предназначены для внутреннего интерьера помещений.
- Экстерьерную ковку. То есть наружную. Изделия предназначены для использования снаружи зданий.
Ковка как таковая с самого своего рождения подразумевала предварительный нагрев рабочего металла перед тем, как человек начинал придавать ему необходимые формы и объемы. Сначала человек, только учившись укрощать металл, даже не думал создавать какие-то украшательства. Он изготавливал прежде всего вещи, которые ему были необходимы для повседневного использования, помогали ему в добыче пропитания и т.
Холодная художественная ковка металла стала отдельным направлением ковки. Появился этот метод ковки вместе с развитием механики. Инженеры того времени изобрели специальные станки и приспособления к ним, которые позволяли из прутков и проката различных форм и профилей получать различные элементы и изделия методом холодной деформации.
Этими первыми методами были штамповка и вальцовка. К тому времени опытные кузнецы, используя классические методы ковки научились изготавливать поразительные высокохудожественные изделия. Естественно, что они стали экспериментировать и учиться делать нечто подобное используя и осваивая новый способ художественной холодной ковки металла.
С помощью специальных станков и приспособлений к ним методом вальцовки мастера стали изготавливать различные декоративные элементы.
Применение холодной ковки
Этот способ широко и практически повсеместно используется для изготовления:
- Ажурных заборов, оград, решеток для окон и балконов.
- Декоративных элементов и панно для фасадов зданий.
- Садовой и парковой мебели.
- Садовых и парковых беседок.
- Уличных фонарей и люстр для помещений.
- Полок и стеллажей.
- Вешалок для одежды.
- Перил для лестничных маршей.
- Мангалов.
- Навесов и козырьков и многого другого.
Самые сложные конструкции выполняются с помощью соединения отдельных частей и элементов при помощи сварки, болтов, заклепок и т. д.
К плюсам художественной холодной ковки металлов можно отнести:
- Удешевление обработки металла, т.к. нет необходимости сооружать горн для предварительного разогрева заготовки и приобретать недешевое оборудование.
- Легкость придания заготовке необходимой конфигурации; готовые элементы не требуют очистки от окалины и копоти ввиду отсутствия таковых.
- Получение абсолютно идентичных деталей и декоративных элементов; это особенно важно при изготовлении изделий с орнаментами.
- Повышенная прочность холоднокованых изделий, т.к. они не подвергались внешнему высокотемпературному воздействию.
Есть у этого способа и минусы:
Для придания заготовке необходимой конфигурации необходимо прикладывать значительные усилия. Но при использовании специальных станков этот недостаток нивелируется полностью.
Финансовые затраты на приобретение специальных станков и оборудования. Но если ковкой заниматься профессионально, затраты окупаются довольно быстро.
Про холодную ковку
Главная О компании Статьи Про холодную ковку
Холодная ковка – это не только менее трудоемкий, но и более экономичный технологический процесс по изготовлению кованых изделий. Она предназначена для получения изделий и деталей из листового или сортового металла, которые можно тиражировать. В основу заложена работа с холодным металлом: заготовки подвергаются механической обработке без предварительного нагрева. В процессе холодной ковки есть возможность изгибать или вырезать детали по трафарету, что значительно облегчает процесс изготовления большой партии кованых изделий а также сокращает сроки и трудозатраты на их производство. Надо отметить, что в некоторых случаях здесь также предполагается нагрев металла, однако заготовки нагреваются лишь в местах стыков и швов для сглаживания шероховатостей. Художественная ковка как способ обработки металла для придания ему необходимой формы и размеров производится по двум основным технологиям – горячая ковка и холодная ковка.
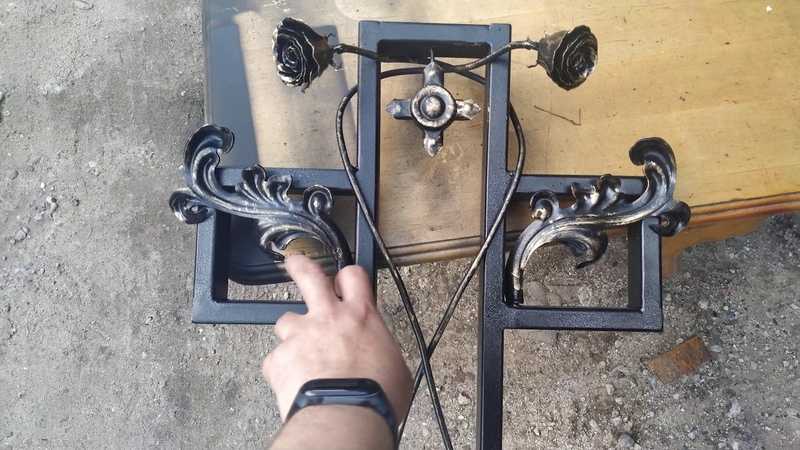


Холодная ковка для металлических деталей, которые вам нужны
Вы являетесь специалистом в области производства, ответственным за планирование, приобретение или определение компонентов ваших сборок? Если это так, то вы, несомненно, знакомы с треугольником цена-время-качество. Чтобы сохранить свой бизнес, вы должны сбалансировать все три составляющие: низкая стоимость, высокое качество и доставка. Будет только хуже, если вы этого не сделаете. Вы отстанете в гонке.
«Кто-то сделает ваш продукт устаревшим. Убедитесь, что это вы». — Эдвин Лэнд.
Холодная ковка может дать вам необходимое конкурентное преимущество.
Содержание
Что такое холодная ковка? Холодная ковка — это технология обработки металлов, при которой прутковый прокат обрабатывается и выдавливается в открытый штамп. Этот метод происходит при температуре окружающей среды или ниже температуры рекристаллизации металла, чтобы придать металлу желаемую форму.
Холодная ковка является эффективным и экономически выгодным методом формовки металла для изготовления больших объемов деталей с низкими затратами. Способ ковки разный в зависимости от температуры: холодный или горячий. Осуществляется на станках с молотками или на прессах для профилирования, прессования и прокатки стали.
Этот метод сравнительно менее затратен, чем горячая ковка, так как конечный продукт требует очень мало отделочных работ. Хотя холодная ковка называется холодной, она происходит при комнатной температуре или близкой к ней.
Размер станков для холодной штамповки зависит от твердости материала и веса конечного обрабатываемого компонента.
Холодная ковка обеспечивает экономию материала до 70% производственных затрат, так как очень мало отходов и брака.
Как работает холодная ковка? Низкая стоимость ковки обусловлена снижением трудозатрат и устранением второстепенных операций. Детали могут быть изготовлены быстро и эффективно со скоростью до 1000 штук в час, что снижает затраты.
Холодная ковка позволяет получить почти идеальное качество поверхности с повышенной размерной стабильностью. Каждая операция повышает прочность и долговечность заготовки, делая компоненты долговечными.
Ковка может относиться к процессу формирования металла в твердой форме. Большая часть ковки осуществляется посредством процесса осадки. Молотки или домкраты горизонтально вдавливают в концы, чтобы расширить или изменить форму заготовки.
Части обычно проходят стадию за станциями, пока не приобретут окончательную форму. Болты более высокой прочности традиционно подвергаются холодной головке с использованием этого метода. Клапан автомобильного двигателя формируется в процессе принудительной ковки. При штамповке детали выковываются в штампах для получения готовых изделий с помощью большого молота, прикрепленного к машине.
На фото выше: холоднокованый приводной вал.
Ковка — типичная производственная процедура, при которой сжимающие силы могут формировать металлические детали. Ковка возможна в разных условиях, например, горячая или холодная ковка. В ковке используются молотки или прессы, которые сжимают и деформируют материалы в твердые куски.
Наиболее существенная разница между горячей и холодной ковкой заключается в температуре. В отличие от холодной ковки, которая начинается при температуре окружающей среды, процесс горячей ковки происходит, когда металл нагревается выше температуры его кристаллизации. Высокая температура горячей штамповки помогает предотвратить деформационное упрочнение. При таких температурах металлы пластичны, хотя технически тверды.
Холодная ковка — жизненно важный процесс придания формы и упрочнения металла.
В отличие от этого, горячая штамповка позволяет получить материал с превосходным пределом текучести, меньшей твердостью, более высокой пластичностью и более высокой прочностью материалов.
Вы можете выбрать один из двух типов на основе экономических показателей, ваших требований к механическим свойствам и размера оборудования, необходимого для изготовления детали определенного размера и объема.
Примечание. Ковка полностью отличается от литья, когда расплавленный материал заливают в формы.
Холодная штамповка и ковка – одно и то же?Процессы металлообработки включают штамповку и ковку. Оба они включают модификацию металла для получения различных размеров и/или форм. Доступны различные металлы и сплавы, от железа и стали до алюминия, бронзы и т. д. Несмотря на то, что они используют различные методы изменения металла, штамповка и ковка — это не одно и то же.
Что формируется? Деформирование металлической заготовки с помощью механической деформации называется формованием. По определению, слово «формование» относится к любому металлургическому процессу, включающему деформацию металлической заготовки механическими средствами. Термин «формование» в соответствии с его точным значением относится к любой операции металлообработки, при которой металлическая заготовка деформируется физическими средствами. Поскольку во время формовки материал не добавляется и не удаляется из заготовки, она не меняет свой вес, а только форму.
Металлообработка имеет два вида штамповки: сжатие и растяжение. Сжимающая нагрузка используется для изгиба металлических деталей за счет деформации сжатия, тогда как растягивающее напряжение используется для деформации металлических компонентов. Прокатка и экструзия являются примерами формования сжатием, поскольку они используют сжимающую силу. С другой стороны, растяжение и опускание являются примерами деформации растяжением, поскольку они подвергают металлические изделия растягивающему напряжению.
Что такое ковка? Процесс ковки — это технология металлообработки, в которой используются удары под давлением для придания формы металлической заготовке и изменения ее формы. Все кузнечные операции предполагают использование мощных и напорных ударов для деформации и модификации металлической заготовки.
Металлические детали могут быть изменены по размеру и/или форме путем штамповки или ковки. Ковка предполагает нанесение сильных ударов по металлическим деталям для придания им формы, тогда как формование достигается за счет механической деформации. В любом подходе нет отходов, что делает их экономически эффективными, если вы работаете с дорогими материалами. Чтобы выяснить, какая процедура будет лучше всего соответствовать геометрии, объему и механическим требованиям вашего конечного компонента, вам следует проконсультироваться со специалистом.
Какие материалы лучше всего подходят для процесса холодной ковки? Когда дело доходит до выбора металла для проекта, есть много вариантов. Примерами таких материалов являются твердые металлы, такие как углеродистая сталь, легированная сталь и нержавеющая сталь. Алюминий, латунь, медь, кремний и магний являются мягкими металлами, которые можно использовать. Единственным требованием для любого металла является твердость по Роквеллу 44 HRC или ниже.
Вверху: Болты с лезвиями, изготовленные методом холодной ковки.
В каких отраслях применяется холодная ковка?Автомобильный, аэрокосмический, сельскохозяйственный, внедорожный, судовой, трубопроводный и ручной инструмент — и это лишь некоторые из них.
Размеры варьируются от нескольких унций до тысяч фунтов.
Автомобильная промышленность: например, компоненты подвески, такие как шпиндели промежуточных рычагов, и элементы двигателя, такие как шатуны и редукторы, изготавливаются методом холодной ковки. Холоднокованые детали из-за их выдающейся ударопрочности используются в местах с высокими нагрузками. Компоненты холодной ковки включают в себя такие элементы, как трансмиссия, карданные валы, стойки или амортизаторы.
Трубопровод: Штоки трубопроводов и корпуса клапанов, которые часто состоят из медного сплава для повышения коррозионной стойкости, изготовлены методом холодной ковки.
Ручные инструменты и скобяные изделия: гвозди, винты, заклепки и болты являются примерами крепежных изделий. Жесткие допуски и высокая точность размеров делают ковку лучшим вариантом по сравнению с другими процессами, такими как механическая обработка. Ручные инструменты, такие как розетки, часто подделываются.
Военные: Холодная ковка используется при изготовлении гильз, пуль и другого военного снаряжения в соответствии со строгими военными стандартами. Компоненты холодной ковки обеспечивают превосходную надежность и производительность, которые требуются военным. Детали с жесткими допусками и прочностью идеально подходят для боевого оружия.
Зубчатые колеса: холодная ковка используется для производства зубчатых колес, поскольку она устраняет необходимость в большей части механической обработки или придания формы зубчатым колесам. Важным преимуществом холоднокованых шестерен является то, насколько плавно и бесшумно они входят в зацепление (по зубьям шестерни, обработанным механической обработкой).
Для производства большого количества деталей по низкой цене холодная ковка является успешным и экономичным методом деформации металла.
Холодная ковка производится на станках, предназначенных для деформации и придания формы металлу.
Вы сэкономите деньги на всем, от материалов до времени. Из-за небольшого количества образующегося лома (по сравнению с процессами удаления металла) вы можете сэкономить до 70% на материалах. Стоимость единицы продукции значительно снижается, поскольку компоненты изготавливаются очень быстро.
Вам нужно подумать о размере детали (и весе), а также о жесткости материала и объемах производства. Эксперт в этой области может предложить вам несколько вариантов, которые помогут вам принять решение.
Часто задаваемые вопросы Что подразумевается под холодной ковкой? Холодная ковка стала популярным процессом штамповки без стружки. Обычно это не требует никакой другой работы, кроме сверления. Наиболее широко используемое определение предполагает изготовление или ковку объемного материала с нулевым нагревом заготовки.
Он имеет много преимуществ по сравнению с горячей ковкой, таких как жесткие допуски на размеры, высокое качество обработки поверхности и использование более дешевых материалов.
Каковы преимущества холодной ковки?При холодной ковке нагревание не требуется. Этот метод ковки обеспечивает повышенную взаимозаменяемость и воспроизводимость. Вы можете добиться превосходного качества поверхности, минимальных проблем с загрязнением, улучшенного контроля размеров и большей прочности в результате улучшения направленности волокон.
Каковы недостатки холодной ковки? Недостаток холодной ковки заключается в том, что она не подходит для некоторых материалов, поскольку она может вызвать растрескивание во время производства, создать нежелательное остаточное напряжение, а кованые металлы часто менее пластичны. Специалист в этой области может помочь вам выбрать один из нескольких вариантов.
Независимо от того, изучаете ли вы варианты для нового продукта или у вас есть существующий продукт, который вы хотели бы запустить в производство, Federal Group USA предоставит вам данные и инструменты, необходимые для принятия обоснованного решения о поиске поставщиков. ваш следующий продукт, оптимизированный для вашего производственного процесса.
Более 41 года мы также предоставляем высококачественные услуги по контрактному производству для самых разных отраслей. Свяжитесь с нами сегодня, чтобы узнать больше.
Холодная ковка стали — Knife Steel Nerds
Спасибо Марко Гульдиманну, Даррину Томасу, Джейсону Тиллоссону, Доминику Паолантонио, Кену, Бенедикту Питерсу и Стиву Грейнеру за то, что они стали сторонниками Knife Steel Nerds на Patreon!
Холодная ковка
Холодная ковка очень похожа на горячую ковку, за исключением того, что она производится при комнатной температуре или близкой к ней.
Однако внутри стали много зерен, и границы между этими зернами проходят там, где встречаются плоскости атомов. Каждое зерно имеет различную «ориентацию» относительно других, что представлено линиями сетки в зернах на схеме ниже:
Во время холодной прокатки мы спекаем эти зерна и удлиняем их. При ковке куска стали деформация, конечно, не такая равномерная, но принципы в основном те же.
Одновременно происходит упрочнение стали в процессе холодной обработки давлением. По мере обработки стали образуются «дислокации».
Прочность металлов зависит от того, насколько легко могут двигаться дислокации. Различные функции могут предотвратить движение дислокаций, таких как границы зерен. Таким образом, мелкое зерно с большим количеством границ зерен приводит к более высокой прочности, поскольку дислокации блокируются этими границами. Дислокации также не могут легко перемещаться через другие дислокации, поэтому более высокая плотность дислокаций означает более высокую прочность, потому что их больше, что блокирует движение других. Мартенсит получает свою прочность отчасти из-за очень высокой плотности дислокаций. О том, что делает мартенсит прочным, вы можете прочитать в этой статье. По мере холодной обработки стали образуется все больше и больше крошечных атомных дефектов, называемых дислокациями, и чем выше плотность этих дислокаций, тем прочнее сталь. Эти дислокации не следует рассматривать как макроскопические дефекты или крошечные трещины; дислокации не плохи, они присущи металлам, так как атомная структура никогда не будет идеальной. Возможно, лучше рассматривать это как увеличение степени несовершенства кристаллической структуры за счет холодной обработки. Холодная обработка обычно указывается в процентах, т.е. 10 % холодной обжатия означает, что толщина была уменьшена на 10 %, а 50 % означает, что толщина уменьшилась вдвое, с соответствующим увеличением длины, конечно.
Вот увеличение твердости отожженной модстали А8 после холодной обработки деформацией до 50 % [1]:
Когда мы начинаем с отожженной стали с мягким ферритом и карбидами, структура выглядит примерно так, как показано ниже, с относительно круглыми ферритными зернами вместе с более мелкими карбидами (карбиды разных цветов, чтобы различать):
Отожженная нержавеющая сталь 13C26 [2], черная полоса 5 микрон
Приведенное выше изображение было получено с помощью «дифракции обратно рассеянных электронов» (EBSD), которая способна различать различные фазы (аустенит, феррит, карбиды) и ориентацию зерен. Также видна относительная плотность дислокаций, поскольку зерна с низкой плотностью являются «чистыми», а зерна с высокой плотностью дислокаций более грубые и темные.
При холодной прокатке стали карбиды более или менее не затрагиваются, но зерна удлиняются и плотность дислокаций увеличивается, что видно на изображении ниже, поскольку «качество изображения» зерен хуже:
13C26 после небольшого холодного обжатия [2], на этом изображении карбиды не окрашены, черная полоса 2 микрона
13C26 после большого холодного обжатия [2], черная полоса 5 микрон
При нагревании до достаточно высокой температуры сталь «перекристаллизуется», то есть образует новые зерна. Чем больше энергии вкладывается в сталь (большее холодное обжатие), тем выше движущая сила рекристаллизации. Эта энергия накапливается в стали в основном за счет образования дислокаций. Таким образом, энергия высвобождается из стали за счет образования новых зерен с низкой плотностью дислокаций. Процесс перекристаллизации вы можете увидеть на видео ниже:
Вы можете видеть, что металл в начале видео имеет большую структуру, затем начинают формироваться новые «чистые» зерна. Если вы внимательно посмотрите, то увидите, что на белых частицах образуются новые зерна, которые ведут себя подобно карбидам в стали. Карбиды способствуют зарождению рекристаллизованных зерен, но они также могут закреплять рекристаллизующиеся зерна, поэтому взаимодействие карбидов и рекристаллизации является относительно сложным.
Рекристаллизация происходит за счет диффузии атомов железа, поэтому для достаточной диффузии требуется определенная температура. Вот почему холодная обработка имеет такой эффект, потому что температура настолько низка, что сталь не может «зафиксироваться» диффузией. Однако температура, при которой начинается рекристаллизация, также определяется степенью наклепа. Чем выше степень наклепа, тем ниже температура начала рекристаллизации [3]:
При холодной обработке в несколько процентов стали, показанной выше, для начала рекристаллизации требуется полная температура 700°C (1300°F), в то время как при 50-70% холодном обжатии требуется только 500°C (930°F). необходимые для рекристаллизации. Чем больше холодная обработка, тем больше энергии вложено в сталь в виде дислокаций, и эта энергия увеличивает «движущую силу» рекристаллизации. На скорость рекристаллизации также влияет температура: при более высоких температурах диффузия ускоряется, поэтому скорость рекристаллизации также увеличивается [4]:
Вы можете видеть, что для указанной выше стали рекристаллизация завершается в течение 20 секунд при 760°C, а при 650°C она занимает более 500 секунд. Опять же, эта скорость при разных температурах зависит от состава, карбидов и степени холодной обработки, но приведенный выше пример дает некоторое визуальное представление о разнице в зависимости от температуры.
Холоднокатаная сталь
Вся эта информация актуальна, поскольку некоторые ножевые стали доступны в холоднокатаной форме, что может привести к некоторым отличиям от горячекатаной стали. Существует множество причин, по которым может быть желательна холоднокатаная сталь, например, улучшение состояния поверхности. Как правило, холоднокатаная сталь имеет яркую блестящую поверхность без окалины. Сталь сначала «протравливается», проходит через ванну с кислотой для удаления окалины перед холодной прокаткой, и сочетание этих двух процессов придает стали очень гладкую поверхность. Толщина стали обычно также более постоянна, и холоднокатаная сталь часто доступна в более тонких размерах. AEB-L обычно доступен в холоднокатаной форме, а некоторые 1095 стали, среди прочего.
Приводит ли холодная ковка к превосходным конечным свойствам?
После всех этих воздействий на сталь во время холодной обработки и рекристаллизации, как это влияет на окончательную термообработку аустенитизации и закалки, а затем на результирующие твердость и ударную вязкость? Процесс холодной ковки и рекристаллизации может привести к уменьшению размера зерна, что может улучшить баланс твердости и ударной вязкости. Вы можете прочитать о том, почему в этой статье о переработке зерна. Это уже третий раз, когда я ссылаюсь на эту статью, и я очень надеюсь, что вы ее прочитали. Уменьшение размера зерен феррита увеличивает количество центров зародышеобразования для образования аустенита, так что окончательный размер исходного аустенитного зерна также становится меньше.
Меньший размер зерна феррита приводит к большему количеству зародышей аустенита (синие кружки), поэтому, когда аустенит растет и замещает феррит, размер зерна меньше
В одном исследовании стали 52100 [5] они обнаружили, что 50%
В другом исследовании 52100 [6] было обнаружено, что холодная прокатка уменьшила конечный размер зерна, а также что энергия наклепа ускорила растворение карбидов:
Увеличение растворения карбида при высокой температуре означает, что в растворе больше углерода. Большее количество углерода в растворе перед закалкой приводит к более высокой твердости и меньшей ударной вязкости (подробнее см. Аустенитизация, часть 1 и часть 2). Однако, поскольку размер зерна также был уменьшен, произошло улучшение как твердости, так и ударной вязкости за счет холодного обжатия стали 52100 перед термической обработкой:
обработки, вот изображения границ зерен из вышеприведенных экспериментов:
Другое исследование аустенитного отпуска стали 52100 [7] для бейнитной микроструктуры показало, что холодное обжатие перед термической обработкой привело к улучшению ударной вязкости:
стали, а также 10% и 20% холодного обжатия перед термической обработкой. Они подвергались аустенизации при 1030°C (1885°F) в течение 20 минут перед закалкой, а затем измеряли твердость и наблюдали за микроструктурой. Они обнаружили, что холодная обработка ускоряет растворение карбида и уменьшает размер зерна, как в исследовании 52100. Однако твердость снизилась, поскольку образовалось больше остаточного аустенита. Больше углерода и сплава в растворе от растворения карбида может увеличить остаточный аустенит, вы можете узнать, почему в этой статье. Уменьшение размера зерна также снижает начальную температуру мартенсита и, следовательно, увеличивает конечный остаточный аустенит [9].]. Следовательно, использование холодной прокатки может потребовать снижения выбранной температуры аустенизации, чтобы гарантировать отсутствие избыточного остаточного аустенита после термообработки.
Испытания на ударную вязкость не проводились, но вы можете видеть уменьшение размера зерна на этих микрофотографиях:
Опасность холодной прокатки вероятность растрескивания при холодной прокатке. Это часто происходит из-за растрескивания краев и, в некоторых случаях, «аллигаторизации», когда сталь откалывается от центра:
Это изображение из [9]
Аллигаторная обработка начинается с образования пустот вблизи центра стали, которые в конечном итоге соединяются, пока сталь не расколется:
Эти изображения из [9]
Инструментальные стали с их высокой долей карбидов может привести к продвижению этих пустот, так что с большей вероятностью произойдет аллигаторное образование. Высокая доля карбидов также означает, что пластичность отожженной стали в целом низкая. Поэтому степень холодного обжатия, которую может выдержать инструментальная сталь, относительно низка. В случае A8 мод наблюдалось образование трещин по центральной линии с уменьшением до 20% [9].]. Следовательно, стали с небольшим содержанием мелких карбидов, такие как AEB-L, 1095 или 52100, будут демонстрировать лучшую пластичность при холодной прокатке, чем стали с большим содержанием карбидов, такие как стали D2 или 10V.
Другим частым дефектом холодной прокатки стали является растрескивание кромок [10]:0095
Я не знаю многих производителей ножей, которые намеренно ковали сталь холодным способом. Мюррей Картер, вероятно, самый известный пример того, кто это делает. Холодная ковка — традиционный процесс для японских кузнецов, где он и изучил эту технику. Картер утверждает [11], что он использует холодную ковку для улучшения качества поверхности и окончательной формы и плоскостности в большей степени, чем это возможно при высокотемпературной ковке. Он также утверждает, что холодная ковка приводит к «лучшему балансу между остротой кромки, сохранением кромки и простотой заточки». В видеодемонстрации он сказал, что холодная ковка улучшила окончательную структуру зерна. Поскольку это традиционная техника, может быть трудно понять, каковы были первоначальные причины холодной ковки, я думаю, что улучшение плоскостности и формы более вероятно, чем преднамеренное улучшение размера зерна или конечных свойств. Следует признать, что большинство ножей Carter ламинированы более мягкой сталью или железом (сан-май), что может сделать сталь менее восприимчивой к растрескиванию. Чтобы попрактиковаться в холодной ковке перед изготовлением готовых ножей, он рекомендует намеренно холодную ковку стали до тех пор, пока она не треснет, чтобы лучше понять, сколько сталь может выдержать.
Резюме и выводы
Холодное обжатие приводит к увеличению твердости стали за счет увеличения плотности дислокаций. При нагревании сталь рекристаллизуется, образуя новые зерна, и эти зерна часто меньше, чем первоначальный размер зерна. Измельчение размера зерна поддерживается за счет окончательной термообработки до мартенсита. Уточнение размера зерна может привести к повышению ударной вязкости. Холодное обжатие также приводит к ускорению растворения карбида, а это означает, что может потребоваться снижение температуры аустенитизации для сохранения той же твердости. Инструментальные стали имеют относительно низкую пластичность при комнатной температуре, поэтому холодное обжатие должно быть ограничено до 15% или менее, если оно выполняется, и только на отожженной стали.
[1] Гасеми-Нанеса, Хади, Мохаммад Джахази, Маджид Хейдари и Том Левассер. «Влияние вызванных деформацией микропустот на механическое разрушение мартенситной инструментальной стали AISI A8-Mod». В материалах конференции AIP , vol. 1896, нет. 1, с. 020021. Издательство AIP, 2017.
[2] Ионеску-Габор, Сорин. «Исследование и эмпирическое моделирование рекристаллизационного отжига полосы мартенситной хромистой стали с помощью EBSD». Докторская диссертация, KTH, 2009.
[3] Х. Ф. Кайзер и Х. Ф. Тейлор, Транзакции Американского общества металлов, том. 27, с. 256 (1939).
[4] Ян, Дза, Э. Л. Браун, Д. К. Мэтлок и Г. Б. Краусс. «Рекристаллизация феррита и образование аустенита в холоднокатаной стали с межкритическим отжигом». Металлургические операции А 16, вып. 8 (1985): 1385-1392.
[5] Бесвик, Дж. М. «Свойства разрушения и распространения усталостных трещин в закаленной стали 52100». Металлургические операции А 20, № 10 (1989): 1961-1973.
[6] Ли, Чжэнь-син, Чан-шэн Ли, Цзинь-и Жэнь, Бин-чжоу Ли, Цзянь Чжан и Юн-цян Ма. «Влияние холодной деформации на микроструктуру и ударную вязкость в процессе аустенизации подшипниковой стали 1,0 C–1,5 Cr». Материаловедение и инженерия: A 674 (2016): 262–269.
[7] Чакраборти, Дж., П. П. Чаттопадхьяй, Д. Бхаттачарджи и И. Манна. «Микроструктурное усовершенствование бейнита и мартенсита для повышения прочности и ударной вязкости высокоуглеродистой низколегированной стали».